Texturing liquid for crystalline silicon and preparation method thereof
A technology for making texturing liquid and crystal silicon, which is applied in chemical instruments and methods, crystal growth, single crystal growth, etc. It can solve the problems that the surface of the silicon wafer cannot obtain contact with it, the concentration of the reactant -OH is reduced, and the production cost cannot be reduced, etc. problems, to achieve the effects of reducing environmental pollution and waste water treatment costs, stabilizing the solution system, and broadening the process tolerance range
- Summary
- Abstract
- Description
- Claims
- Application Information
AI Technical Summary
Problems solved by technology
Method used
Examples
Embodiment 1
[0034] Add deionized water into the reaction kettle, according to the mass percentage, dissolve 30% sodium hydroxide in deionized water, then add 0.2% isopropanol and 0.4% absolute ethanol in turn, and then pour the mixed solution into the storage tank and add 5% liquid carbon dioxide and 2% alkali catalyst at the same time, then pressurize the storage tank, and finally add 5% sodium hypochlorite and 3% sodium citrate, fructose sodium and lignosulfonate to 1 : 1:3 non-ionic surfactant composed of 3 parts by mass to obtain the texturing liquid.
[0035] Use this texturing liquid to make texture on crystal silicon, keep the texture temperature at 80°C, and the texture time is 30 minutes. After the texture is completed, the thickness of crystal silicon is reduced by 6.3 microns, the corrosion effect is better, the reflectivity is reduced, and the corrosion The pits are more uniform.
Embodiment 2
[0037] Add deionized water into the reaction kettle, according to the mass percentage, dissolve 50% sodium hydroxide in deionized water, then add 0.5% isopropanol and 0.8% absolute ethanol in turn, then pour the mixed solution into the storage tank In, and add 10% liquid carbon dioxide and 5% alkali catalyst simultaneously, carry out pressurized filtration to storage tank then, finally add 10% sodium hypochlorite and 8% sodium citrate, fructose sodium and lignosulfonate to 1 : 1:3 non-ionic surfactant composed of 3 parts by mass to obtain the texturing liquid.
[0038] Use this texturing liquid to make texture on crystal silicon, keep the texture temperature at 80°C, and the texture time is 30 minutes. After the texture is completed, the thickness of crystal silicon is reduced by 6.7 microns, the corrosion effect is better, the reflectivity is reduced, and the corrosion The pits are more uniform.
Embodiment 3
[0040] Add deionized water into the reaction kettle, according to the mass percentage, dissolve 40% sodium hydroxide in deionized water, then add 0.3% isopropanol and 0.6% absolute ethanol in turn, then pour the mixed solution into the storage tank and add 8% liquid carbon dioxide and 3% alkali catalyst at the same time, then pressurize the storage tank, and finally add 7% sodium hypochlorite and 5% sodium citrate, sodium fructose and lignosulfonate to 1 : 1:3 non-ionic surfactant composed of 3 parts by mass to obtain the texturing liquid.
[0041] Use this texturing liquid to make texture on crystal silicon, keep the texture temperature at 80°C, and the texture time is 30 minutes. After the texture is completed, the thickness of crystal silicon is reduced by 6.5 microns, the corrosion effect is better, the reflectivity is reduced, and the corrosion The pits are more uniform.
[0042] The reaction principle of crystalline silicon texturing is shown in the equation: Si+2NaOH+H...
PUM
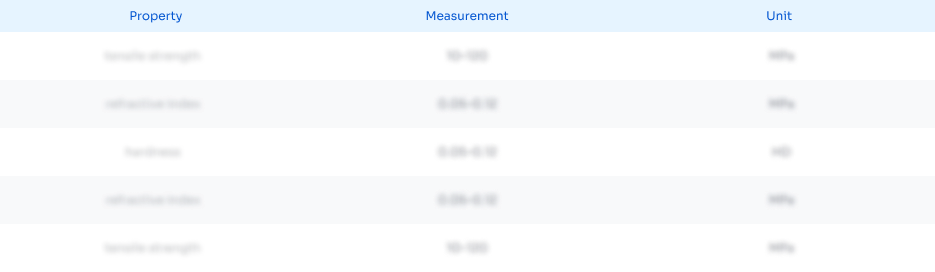
Abstract
Description
Claims
Application Information

- Generate Ideas
- Intellectual Property
- Life Sciences
- Materials
- Tech Scout
- Unparalleled Data Quality
- Higher Quality Content
- 60% Fewer Hallucinations
Browse by: Latest US Patents, China's latest patents, Technical Efficacy Thesaurus, Application Domain, Technology Topic, Popular Technical Reports.
© 2025 PatSnap. All rights reserved.Legal|Privacy policy|Modern Slavery Act Transparency Statement|Sitemap|About US| Contact US: help@patsnap.com