Method for producing manganese metal through electrolysis
A technology for electrolytic manganese metal and a production method, which is applied in the direction of metal material coating technology and other directions, can solve the problems of increasing difficulty in electrolytic manganese production, reducing the purity of electrolytic manganese, and small profit margins, so as to reduce the harm to the human body and the impact on the environment. The effect of pollution, speed up and precipitation rate, and speed up settling speed
- Summary
- Abstract
- Description
- Claims
- Application Information
AI Technical Summary
Problems solved by technology
Method used
Examples
Embodiment 1
[0027] A production method of electrolytic manganese metal, comprising the steps of:
[0028] (1) Leaching: crush rhodochrosite to obtain rhodochrosite powder; put anolyte into the leaching tank (the anolyte is the waste liquid produced by electrolytic manganese, wherein Mn 2+ The concentration of H is 10g / L, and the concentration of H is 40g / L; NH 4 + The concentration of rhodochrosite powder is 85g / L), add rhodochrosite powder according to the ratio of rhodochrosite powder: anolyte weight ratio of 1:4, fully stir and mix at 55°C for 10 minutes, and then according to rhodochrosite powder: acid weight ratio is Add concentrated sulfuric acid with a mass fraction of 98% at a ratio of 1:0.5, control the reaction temperature at 65°C, and leaching for 8 hours to obtain pulp. At the end of the reaction, check the residual acid content and control the residual acid content of the pulp at 2g / L;
[0029] (2) Iron removal: detection of Fe in the pulp 2+ Content, according to the Fe i...
Embodiment 2
[0036] A production method of electrolytic manganese metal, comprising the steps of:
[0037] (1) Leaching: crush rhodochrosite to obtain rhodochrosite powder; put anolyte into the leaching tank (the anolyte is the waste liquid produced by electrolytic manganese, wherein Mn 2+ The concentration of H is 11g / L, and the concentration of H is 42g / L; NH 4 + The concentration of rhodochrosite powder is 88g / L), according to the ratio of rhodochrosite powder: anolyte weight ratio of 1:4, add rhodochrosite powder, fully stir and mix at 60°C for 5 minutes, and then according to the weight ratio of rhodochrosite powder: acid Add concentrated sulfuric acid with a mass fraction of 98% at a ratio of 1:0.6, control the reaction temperature at 70°C, and leaching for 5.5 hours to obtain pulp. At the end of the reaction, check the residual acid content and control the residual acid content of the pulp at 2.2g / L;
[0038] (2) Iron removal: detection of Fe in the pulp 2+ Content, according to ...
Embodiment 3
[0045] A production method of electrolytic manganese metal, comprising the steps of:
[0046] (1) Leaching: crush rhodochrosite to obtain rhodochrosite powder; put anolyte into the leaching tank (the anolyte is the waste liquid produced by electrolytic manganese, wherein Mn 2+ The concentration of H is 12g / L, the concentration of H is 45g / L, NH 4 + The concentration of rhodochrosite is 90g / L), add rhodochrosite powder according to the ratio of rhodochrosite powder: anolyte weight ratio of 1:4, fully stir and mix at 55-60°C for 8 minutes, and then according to the weight of rhodochrosite powder: acid Add concentrated sulfuric acid with a mass fraction of 98% at a ratio of 1:0.5, control the reaction temperature at 65-70°C, and leaching for 6 hours to obtain pulp. At the end of the reaction, check the residual acid content and control the residual acid content of the pulp at 2.5 g / L;
[0047] (2) Iron removal: detection of Fe in the pulp 2+ Content, according to the Fe in t...
PUM
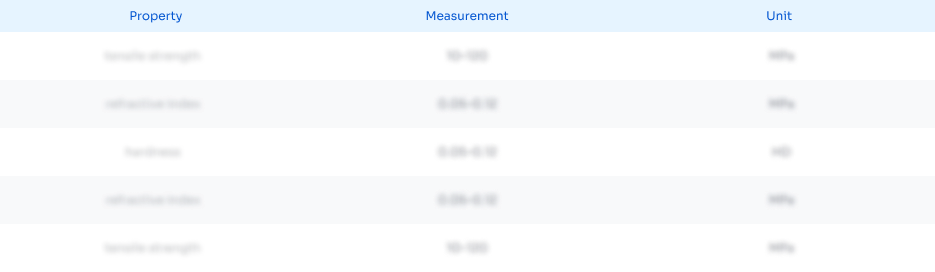
Abstract
Description
Claims
Application Information

- Generate Ideas
- Intellectual Property
- Life Sciences
- Materials
- Tech Scout
- Unparalleled Data Quality
- Higher Quality Content
- 60% Fewer Hallucinations
Browse by: Latest US Patents, China's latest patents, Technical Efficacy Thesaurus, Application Domain, Technology Topic, Popular Technical Reports.
© 2025 PatSnap. All rights reserved.Legal|Privacy policy|Modern Slavery Act Transparency Statement|Sitemap|About US| Contact US: help@patsnap.com