Acrylic acid corrosive enamel
A technology of anti-corrosion enamel and acrylic, which is applied in the direction of anti-corrosion coatings, magnetic coatings, paints containing biocides, etc., and can solve the problems of poor anti-corrosion performance and poor durability
- Summary
- Abstract
- Description
- Claims
- Application Information
AI Technical Summary
Problems solved by technology
Method used
Examples
Embodiment 1
[0012] Example 1 An acrylic anticorrosion enamel, prepared from the following raw materials in weight ratio: 30 parts of acrylic resin, 7 parts of polyethylene glycol, 12 parts of magnesium silicate, 17 parts of calcium propionate, 3 parts of leveling agent, 4 parts of dispersing agent Parts, 4 parts of HEC, 2.5 parts of wetting agent, 4 parts of pigment, 45 parts of deionized water; the following steps are used to prepare: add acrylic resin to the reaction kettle, then add polyethylene glycol, magnesium silicate, calcium propionate in sequence , leveling agent, dispersant, HEC, wetting agent, pigment, deionized water, heat up to 50°C, and fully stir for 3 hours at a speed of 300RPM; S3: After the uniformly mixed material is cooled to room temperature, pass 200 mesh screen.
Embodiment 2
[0013] Example 2 An acrylic anti-corrosion enamel, prepared from the following raw materials in weight ratio: 45 parts of acrylic resin, 16 parts of polyethylene glycol, 22 parts of magnesium silicate, 32 parts of calcium propionate, 11 parts of leveling agent, 13 parts of dispersant Parts, 12 parts of PEO, 8.5 parts of wetting agent, 10 parts of pigment, 60 parts of deionized water; the following steps are used to prepare: add acrylic resin to the reaction kettle, then add polyethylene glycol, filler, calcium propionate, flow Leveling agent, dispersant, PEO, wetting agent, pigment, deionized water, heated up to 70°C, fully stirred at 400RPM for 2h; after the prepared homogeneous mixture was cooled to room temperature, passed 300 mesh screen.
Embodiment 3
[0014] Example 3 An acrylic anticorrosion enamel, prepared from the following raw materials in weight ratio: 37 parts of acrylic resin, 12 parts of polyethylene glycol, 18 parts of magnesium silicate, 26 parts of calcium propionate, 7 parts of leveling agent, 8 parts of dispersant parts, 7 parts of HPAM, 6 parts of wetting agent, 7 parts of pigment, 55 parts of deionized water; the following steps are used to prepare: add acrylic resin to the reaction kettle, then add polyethylene glycol, magnesium silicate, calcium propionate in sequence , leveling agent, dispersant, HPAM, wetting agent, pigment, deionized water, heat up to 60°C, and fully stir for 2.5h at a speed of 350RPM; after the prepared homogeneous mixture is cooled to room temperature, Pass through a 250-mesh sieve.
PUM
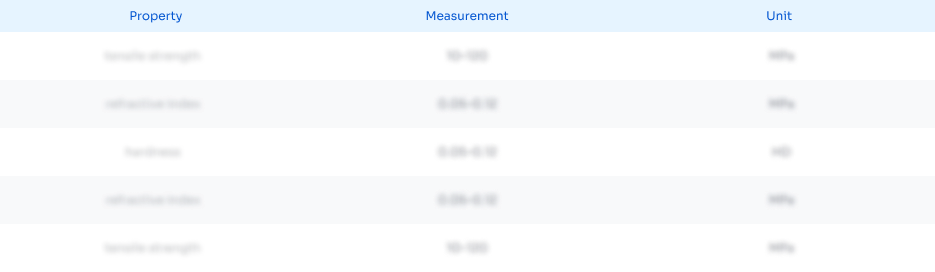
Abstract
Description
Claims
Application Information

- R&D Engineer
- R&D Manager
- IP Professional
- Industry Leading Data Capabilities
- Powerful AI technology
- Patent DNA Extraction
Browse by: Latest US Patents, China's latest patents, Technical Efficacy Thesaurus, Application Domain, Technology Topic, Popular Technical Reports.
© 2024 PatSnap. All rights reserved.Legal|Privacy policy|Modern Slavery Act Transparency Statement|Sitemap|About US| Contact US: help@patsnap.com