Preparation method of low temperature resistant plastic valve sealing ring
A technology of valve sealing and low temperature resistance, applied in the field of plastic materials, can solve the problems of material hardening and leakage, and achieve the effect of easy-to-obtain raw materials, simple process and strong airtight performance
- Summary
- Abstract
- Description
- Claims
- Application Information
AI Technical Summary
Problems solved by technology
Method used
Image
Examples
Embodiment 1
[0019] (1) Combine 15 parts of polysulfone, 6 parts of polyamide, 2 parts of polyoxymethylene, 2 parts of wollastonite, 1 part of butylhydroxyanisole, 3 parts of diphenylamine, 1 part of zinc stearate, three ( 1 part of 2,4-di-tert-butylphenyl) phosphite and 1 part of γ-aminopropylmethyl diethoxysilane were injected into the vacuum reactor and stirred and mixed well at a speed of 2000 rpm, stirred and mixed well 15 After a few minutes, heat to 500°C, continue to react for 30 minutes, and reach the mixture, keep it warm for later use;
[0020] (2) Inject the mixture of step (1) into the injection molding machine to perform injection molding, wherein the barrel of the injection molding machine is four barrels, three barrels, and two barrels in the direction from the feed port to the nozzle. The temperature of the first section of the barrel is 210-215°C, the temperature of the second section of the barrel is 205-210°C, the temperature of the third section of the barrel is 200-205°C...
Embodiment 2
[0025] (1) Combine 16 parts of polysulfone, 7 parts of polyamide, 3 parts of polyoxymethylene, 3 parts of wollastonite, 1 part of butylated hydroxyanisole, 3 parts of diphenylamine, 1 part of zinc stearate, four ( β-(3,5-di-tert-butyl-4-hydroxyphenyl)propionate) 1 part of pentaerythritol ester and 1 part of aniline methyl triethoxysilane are injected into the vacuum reactor and stirred and mixed evenly, the speed is 2000 rpm / Minutes, stir and mix for 15 minutes, then heat to 520°C, continue to react for 30 minutes, to the mixture, keep warm for later use;
[0026] (2) Inject the mixture of step (1) into the injection molding machine to perform injection molding, wherein the barrel of the injection molding machine is four barrels, three barrels, and two barrels in the direction from the feed port to the nozzle. The temperature of the first section of the barrel is 210-215°C, the temperature of the second section of the barrel is 205-210°C, the temperature of the third section of ...
Embodiment 3
[0031] (1) Mix 19 parts of polysulfone, 9 parts of polyamide, 4 parts of polyoxymethylene, 4 parts of wollastonite, 2 parts of butylhydroxyanisole, 4 parts of diphenylamine, 2 parts of zinc stearate, β- 2 parts of (3,5-di-tert-butyl-4-hydroxyphenyl) n-octadecyl propionate and 2 parts of dichloromethyltriethoxysilane are injected into the vacuum reactor and stirred and mixed evenly, the speed is 2000 rpm / Min, stir and mix well for 15 minutes, then heat to 540°C, continue to react for 30 minutes, to the mixture, keep warm for later use;
[0032] (2) Inject the mixture of step (1) into the injection molding machine to perform injection molding, wherein the barrel of the injection molding machine is four barrels, three barrels, and two barrels in the direction from the feed port to the nozzle. The temperature of the first section of the barrel is 210-215°C, the temperature of the second section of the barrel is 205-210°C, the temperature of the third section of the barrel is 200-205...
PUM
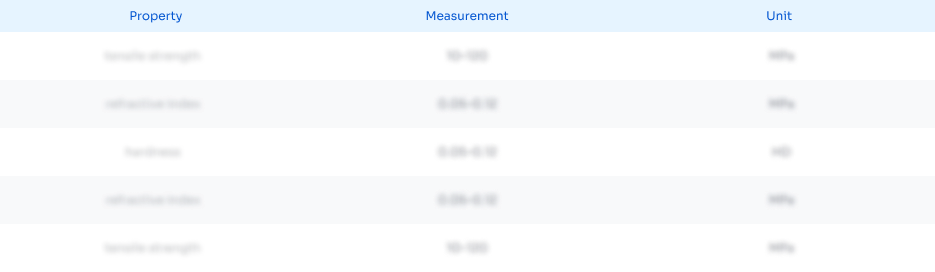
Abstract
Description
Claims
Application Information

- R&D Engineer
- R&D Manager
- IP Professional
- Industry Leading Data Capabilities
- Powerful AI technology
- Patent DNA Extraction
Browse by: Latest US Patents, China's latest patents, Technical Efficacy Thesaurus, Application Domain, Technology Topic, Popular Technical Reports.
© 2024 PatSnap. All rights reserved.Legal|Privacy policy|Modern Slavery Act Transparency Statement|Sitemap|About US| Contact US: help@patsnap.com