A kind of nickel-aluminum-brass alloy and its preparation process
A brass alloy and preparation technology, which is applied in nickel-aluminum brass alloy-related fields, can solve the problems of poor service performance, poor multiple corrosion resistance, general processing technology performance, and difficult processing technology, and achieve excellent corrosion resistance. The effect of improving anti-discoloration ability and improving the quality of thermal blanking
- Summary
- Abstract
- Description
- Claims
- Application Information
AI Technical Summary
Problems solved by technology
Method used
Examples
Embodiment 1
[0026] A nickel-aluminum brass alloy, comprising the following components (by mass percentage): CU: 70%, Al: 2%, Si: 0.5%, Sn: 0.7%, Ni: 0.02%, Mn: 0.05%, and the balance is Zn, said alloy also contains Pb, B and Ce, the mass fractions are respectively Pb: 0.003%, B: 0.003%, Ce: 0.005%, and the total content of the three elements is 0.011%.
[0027] A kind of preparation technology of nickel-aluminum brass alloy, is characterized in that, comprises the following steps:
[0028] Step 1: batching: batching is carried out according to the mass percentage of the above-mentioned materials;
[0029] Step 2: Smelting: use a non-vacuum induction furnace for smelting, the order of alloy addition is: copper-nickel-lead-silicon-manganese-aluminum-zinc-boron-rare earth, during the melting and casting process, the melting temperature is 1140 ° C, boron The composition of rare earth elements and the addition of aluminum elements will cause severe exothermic heat. In order to prevent the po...
Embodiment 2
[0039] A nickel-aluminum brass alloy, comprising the following components (by mass percentage): CU: 72%, Al: 3%, Si: 0.9%, Sn: 1.2%, Ni: 0.1%, Mn: 0.1%, and the balance is Zn, said alloy also contains Pb, B and Ce, the mass fractions are respectively Pb: 0.006%, B: 0.007%, Ce: 0.011%, and the total content of the three elements is 0.024%.
[0040]A preparation process for a nickel-aluminum brass alloy, comprising the following steps:
[0041] Step 1: batching: batching is carried out according to the mass percentage of the above-mentioned materials;
[0042] Step 2: Smelting: Use a non-vacuum induction furnace for smelting. The order of alloy addition is: copper-nickel-lead-silicon-manganese-aluminum-zinc-boron-rare earth. During the melting and casting process, the melting temperature is 1155°C, boron The composition of rare earth elements and the addition of aluminum will cause severe exothermic heat. In order to prevent the possible splashing and injury caused by the addit...
Embodiment 3
[0052] A nickel-aluminum brass alloy, comprising the following components (by mass percentage): CU: 75%, Al: 4%, Si: 1.3%, Sn: 1.5%, Ni: 0.2%, Mn: 0.2%, and the balance is Zn, said alloy also contains Pb, B and Ce, the mass fractions are respectively Pb: 0.01%, B: 0.01%, Ce: 0.015%, and the total content of the three elements is 0.035%.
[0053] A preparation process for a nickel-aluminum brass alloy, comprising the following steps:
[0054] Step 1: batching: batching is carried out according to the mass percentage of the above-mentioned materials;
[0055] Step 2: Smelting: use a non-vacuum induction furnace for smelting, the order of alloy addition is: copper-nickel-lead-silicon-manganese-aluminum-zinc-boron-rare earth, during the melting and casting process, the melting temperature is 1170 ° C, boron The composition of rare earth elements and the addition of aluminum elements will cause severe exothermic heat. In order to prevent the possible splashing and injury caused by...
PUM
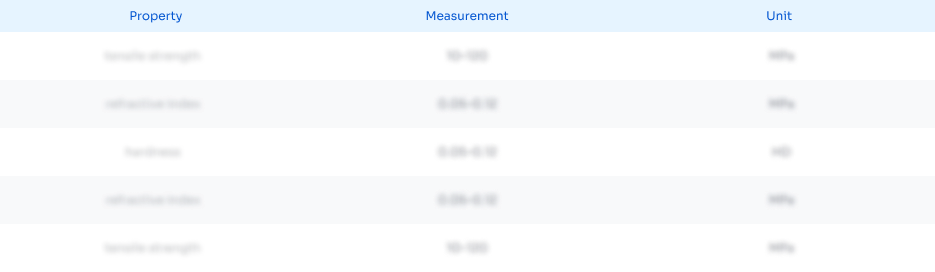
Abstract
Description
Claims
Application Information

- R&D Engineer
- R&D Manager
- IP Professional
- Industry Leading Data Capabilities
- Powerful AI technology
- Patent DNA Extraction
Browse by: Latest US Patents, China's latest patents, Technical Efficacy Thesaurus, Application Domain, Technology Topic, Popular Technical Reports.
© 2024 PatSnap. All rights reserved.Legal|Privacy policy|Modern Slavery Act Transparency Statement|Sitemap|About US| Contact US: help@patsnap.com