Heat treatment method for metal expansion bush
A heat treatment method and metal expansion technology, applied in the field of heat treatment, can solve problems such as sticking to the knife, reduced ductility, and difficulty in drilling, and achieve the effects of easy bending and breaking, reduced wear, and improved drilling efficiency
- Summary
- Abstract
- Description
- Claims
- Application Information
AI Technical Summary
Problems solved by technology
Method used
Image
Examples
Embodiment Construction
[0021] Below in conjunction with accompanying drawing, the present invention is described in further detail:
[0022] The invention relates to a heat treatment method, which heat-treats the metal matrix 2Cr13 of the expansion sleeve through the process of quenching and high-temperature tempering, so that it has good ductility and drillability.
[0023] Such as image 3 As shown, the present invention adopts the quenching and high-temperature tempering process: the workpiece is kept at 1000°C for 1.5 hours, cooled to room temperature in rapid quenching oil when it is taken out of the furnace, and then tempered at 690-750°C for 2.5 hours. Quenching oil for oil cooling. figure 2 The metallographic structure is quenched at 1000°C and tempered at 710°C. The organization is a sorbite organization, and maintains the distribution of martensite needles. Turning chips quenched at 1000°C and tempered at 710°C. Compared with the turning chips after annealing, the cutting chips are ea...
PUM
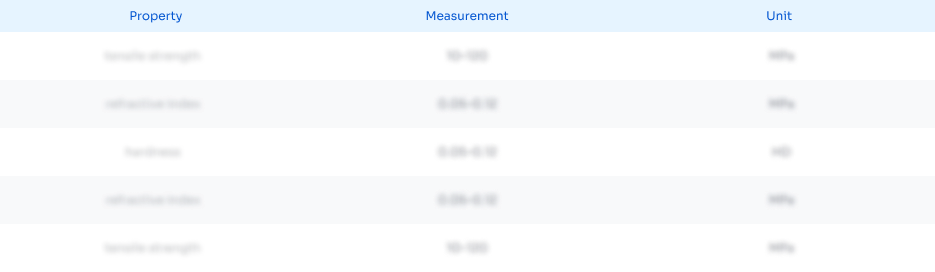
Abstract
Description
Claims
Application Information

- R&D
- Intellectual Property
- Life Sciences
- Materials
- Tech Scout
- Unparalleled Data Quality
- Higher Quality Content
- 60% Fewer Hallucinations
Browse by: Latest US Patents, China's latest patents, Technical Efficacy Thesaurus, Application Domain, Technology Topic, Popular Technical Reports.
© 2025 PatSnap. All rights reserved.Legal|Privacy policy|Modern Slavery Act Transparency Statement|Sitemap|About US| Contact US: help@patsnap.com