Method for preparing chloroiridic acid
A technology of chloroiridic acid and chlorine gas is applied in the field of metallurgy, which can solve the problems of chlorine gas emission and long electrolysis period, and achieve the effects of avoiding passivation, fast reaction speed and promoting transformation.
- Summary
- Abstract
- Description
- Claims
- Application Information
AI Technical Summary
Problems solved by technology
Method used
Image
Examples
Embodiment 1
[0021] Metal iridium powder, of which Ir≥99.5%; analytically pure sodium chloride, of which NaCl content is ≥99.5%; analytically pure soluble starch, of which ignition residue is ≤0.5%; analytically pure hydrochloric acid, of which HCl content is 36.0~38.0%; analytically pure hydrogen Sodium oxide, in which the NaOH content is ≥96.0%; the purity of chlorine gas used is Cl 2 ≥99.5%.
[0022] Weigh 20g of metal iridium powder, mix it evenly with 100g of sodium chloride and 0.5g of starch, and place it in a quartz crucible; place the quartz crucible in a well-type furnace, and then connect a gas absorption device to the flue gas outlet, and the first-stage absorption liquid 500ml of hydrochloric acid solution with a mass concentration of 3%, and the second-stage absorption liquid is 500ml of sodium hydroxide solution with a mass concentration of 20%. When the temperature in the well-type furnace reaches 820°C and the material is in a molten state, start to feed chlorine gas into...
Embodiment 2
[0025] Metal iridium powder, of which Ir≥99.5%; analytically pure sodium chloride, of which NaCl content is ≥99.5%; analytically pure soluble starch, of which ignition residue is ≤0.5%; analytically pure hydrochloric acid, of which HCl content is 36.0~38.0%; analytically pure hydrogen Sodium oxide, in which the NaOH content is ≥96.0%; the purity of chlorine gas used is Cl 2 ≥99.5%.
[0026] Weigh 40g of metal iridium powder, mix it evenly with 240g of sodium chloride and 1.5g of starch, and place it in a quartz crucible; place the quartz crucible in a well-type furnace, and then connect a gas absorption device to the flue gas outlet, and the first-stage absorption liquid They are 1000ml of hydrochloric acid solution with a mass concentration of 5%, and the second-stage absorption liquid is 1000ml of sodium hydroxide solution with a mass concentration of 30%. When the temperature in the well-type furnace reaches 900°C and the material is in a molten state, start to feed chlori...
PUM
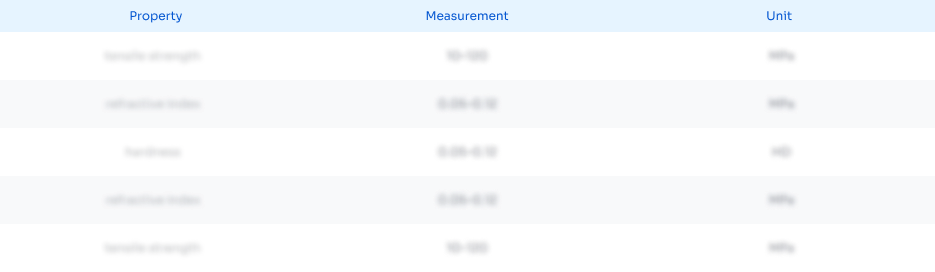
Abstract
Description
Claims
Application Information

- Generate Ideas
- Intellectual Property
- Life Sciences
- Materials
- Tech Scout
- Unparalleled Data Quality
- Higher Quality Content
- 60% Fewer Hallucinations
Browse by: Latest US Patents, China's latest patents, Technical Efficacy Thesaurus, Application Domain, Technology Topic, Popular Technical Reports.
© 2025 PatSnap. All rights reserved.Legal|Privacy policy|Modern Slavery Act Transparency Statement|Sitemap|About US| Contact US: help@patsnap.com