Calibration method for calibrating installation position error of laser distance-measuring sensor
A technology of laser distance measurement and installation position, which is applied in the field of robotics, can solve the problems of sensor part processing error, underutilization of the theoretical position of the sensor, and the installation accuracy of the laser distance measurement sensor cannot meet the demand, so as to avoid local convergence.
- Summary
- Abstract
- Description
- Claims
- Application Information
AI Technical Summary
Problems solved by technology
Method used
Image
Examples
Embodiment approach
[0022] see figure 1 , The device used in the present invention consists of an industrial robot 1, a flat test board 2, a laser ranging sensor 3, a sensor mounting frame 4, and a laser tracker 5. The flat test board 2 is installed at the end of the industrial robot 1, the laser ranging sensor 3 is installed on the sensor mounting frame 4, and the sensor mounting frame 4 remains fixed. There are three reference holes on the plane test plate 2, namely reference hole I, reference hole J, and reference hole K. There are three reference holes on the sensor mounting frame 4, which are respectively reference hole M, reference hole O, and reference hole N, and the connection line between reference hole O and reference hole M is perpendicular to the connection line between reference hole O and reference hole N.
[0023] The steps of the method of the present invention are described in detail below.
[0024] The specific implementation steps of the inventive method are as follows:
[...
PUM
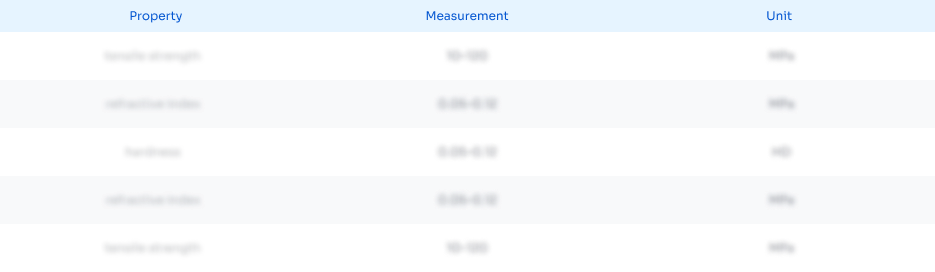
Abstract
Description
Claims
Application Information

- R&D Engineer
- R&D Manager
- IP Professional
- Industry Leading Data Capabilities
- Powerful AI technology
- Patent DNA Extraction
Browse by: Latest US Patents, China's latest patents, Technical Efficacy Thesaurus, Application Domain, Technology Topic, Popular Technical Reports.
© 2024 PatSnap. All rights reserved.Legal|Privacy policy|Modern Slavery Act Transparency Statement|Sitemap|About US| Contact US: help@patsnap.com