Vehicle workpiece non-rigid 3D point cloud registration method based on linear mixed deformation
A technology of 3D point cloud and linear mixing, which is applied in image data processing, instrumentation, computing, etc., and can solve the problem that the ICP method is no longer applicable
- Summary
- Abstract
- Description
- Claims
- Application Information
AI Technical Summary
Problems solved by technology
Method used
Image
Examples
specific Embodiment approach 1
[0033] Specific implementation mode one: combine figure 1 To illustrate this embodiment, the specific process of a non-rigid 3D point cloud registration method for automobile workpieces based on linear hybrid deformation in this embodiment is as follows:
[0034] Step 1: Input the reference point cloud Q' and the source point cloud P' into the program, use the grid filter method to perform down-sampling, and obtain the down-sampled reference point cloud Q and source point cloud P;
[0035] Step 2: Plan the deformed point on the downsampled source point cloud P, that is, the control point, and construct the control vector S; artificially plan, select the point that will be deformed on the downsampled source point cloud P, which is the control point Points, according to the degrees of freedom that these control points may move (each point has three degrees of freedom x, y, z), plan the control vector (define all required variables as a vector, for example, each control point ha...
specific Embodiment approach 2
[0044] Specific embodiment two: the difference between this embodiment and specific embodiment one is: in the step three, the bounded harmonic weight set W is calculated, and the specific process is:
[0045] Minimize the equation:
[0046]
[0047] and satisfy the following constraints:
[0048]
[0049]
[0050]
[0051] where δ jk is the Kronecker function, when j=k, δ jk The value is 1, otherwise δ jk The value is 0; Δω j for ω j Increment; ω j as the control point The corresponding bounded harmonic weights; is the jth control point, j=1,2,...,m, m is the number of control points, and the value of m is a positive integer, is the kth control point, and the value of k is a positive integer, is the point on the source point cloud before deformation, is the jth control point at The weight at , j is the control point, i is the point on the source point cloud P, and the value of i is a positive integer. The control point is the point artificially plan...
specific Embodiment approach 3
[0053] Specific embodiment three: the difference between this embodiment and specific embodiment one or two is: in the step three, a linear mixed deformation model is constructed, and the specific formula is:
[0054]
[0055] in is the point on the deformed source point cloud, ψ j as the control point The rigid body transformation matrix of .
[0056] Other steps and parameters are the same as those in Embodiment 1 or Embodiment 2.
PUM
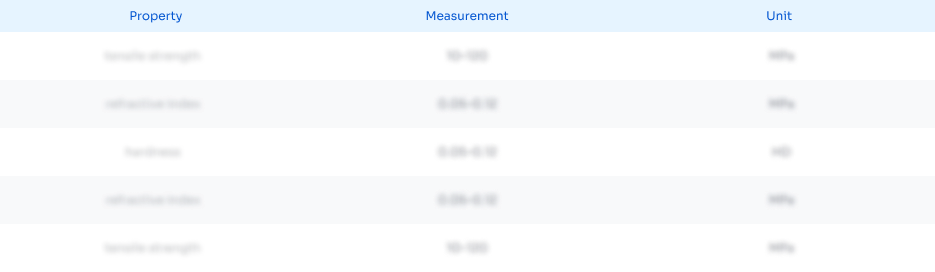
Abstract
Description
Claims
Application Information

- R&D
- Intellectual Property
- Life Sciences
- Materials
- Tech Scout
- Unparalleled Data Quality
- Higher Quality Content
- 60% Fewer Hallucinations
Browse by: Latest US Patents, China's latest patents, Technical Efficacy Thesaurus, Application Domain, Technology Topic, Popular Technical Reports.
© 2025 PatSnap. All rights reserved.Legal|Privacy policy|Modern Slavery Act Transparency Statement|Sitemap|About US| Contact US: help@patsnap.com