High temperature alloy chemical milling fluid and using method thereof
A chemical milling and superalloy technology, applied in the field of superalloy chemical milling fluid, can solve the problems affecting the quality and efficiency of chemical milling, and achieve the effect of small surface roughness, improved machining efficiency and good flatness.
- Summary
- Abstract
- Description
- Claims
- Application Information
AI Technical Summary
Problems solved by technology
Method used
Examples
Embodiment 1
[0009] Embodiment 1: the material of the part to be processed is GH4169 superalloy, at first the part is immersed in a kind of superalloy chemical milling fluid of the present invention, and composition and content are: the concentrated nitric acid 100ml / L of mass fraction 65%, mass fraction 98 % Concentrated sulfuric acid 100ml / L, ferric sulfate 100g / L, hexamethylenetetramine 2g / L, the balance is water, keep the temperature of the chemical milling fluid at 40°C, and make the parts in the chemical milling fluid at a speed of 5r / min Rotate in the middle, and stir the chemical milling fluid at the same time, the stirring speed is 160r / min, take out the parts after 5min, and carry out the post-processing process. Finally, the quality difference of parts before and after chemical milling was measured, and the rate of chemical milling in Example 1 was calculated to be 14 μm / min, and the machined surface had small roughness, good flatness, and no defects such as over-corrosion and st...
Embodiment 2
[0010] Embodiment 2: the part material to be processed is GH4169 superalloy, at first the part is immersed in the preparation concentrated nitric acid volume fraction is 30%, the concentrated sulfuric acid volume fraction is 10%, ferric sulfate is 150g / L, hexamethylenetetramine is 5g / L L chemical milling fluid, keep the temperature of the chemical milling fluid at 45°C, and make the parts rotate in the chemical milling fluid at a speed of 15r / min, while stirring the chemical milling fluid at a stirring speed of 180r / min, take out the parts after 5min, and carry out Processing procedure. Finally, the quality difference of parts before and after chemical milling was measured, and the rate of chemical milling in Example 1 was calculated to be 23 μm / min, and the processed surface had small roughness, good flatness, and no defects such as over-corrosion and streamline pits.
Embodiment 3
[0011] Embodiment 3: the part material GH4169 superalloy to be processed, at first part is immersed in the concentrated nitric acid volume fraction that is 30%, the concentrated sulfuric acid volume fraction is 20%, ferric sulfate is 200g / L, hexamethylenetetramine is 10g / L In the chemical milling fluid, keep the temperature of the chemical milling fluid at 45°C, and make the parts rotate in the chemical milling fluid at a speed of 15r / min, while stirring the chemical milling fluid at a stirring speed of 180r / min, take out the parts after 5min, and perform post-processing process. Finally, the quality difference of parts before and after chemical milling was measured, and the rate of chemical milling in Example 1 was calculated to be 31 μm / min, and the machined surface had small roughness, good flatness, and no defects such as over-corrosion and streamline pits.
[0012] Embodiment 3: the material of the parts to be processed is GH4169 superalloy, first the parts are immersed i...
PUM
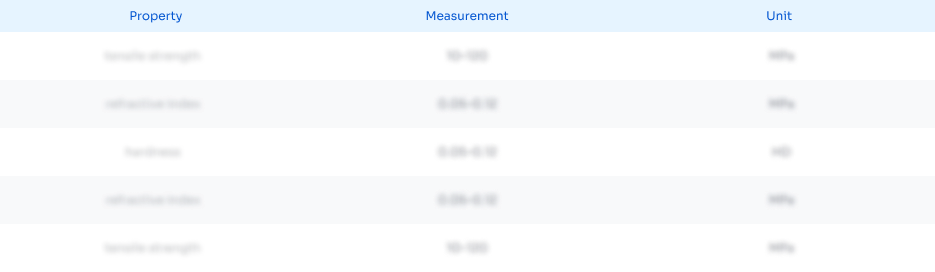
Abstract
Description
Claims
Application Information

- R&D
- Intellectual Property
- Life Sciences
- Materials
- Tech Scout
- Unparalleled Data Quality
- Higher Quality Content
- 60% Fewer Hallucinations
Browse by: Latest US Patents, China's latest patents, Technical Efficacy Thesaurus, Application Domain, Technology Topic, Popular Technical Reports.
© 2025 PatSnap. All rights reserved.Legal|Privacy policy|Modern Slavery Act Transparency Statement|Sitemap|About US| Contact US: help@patsnap.com