Double-smelting dephosphorization process for high-phosphorus molten iron
A molten iron, high phosphorus technology, applied in the manufacture of converters, etc., can solve the problems of slow slag melting, molten steel quality and cost impact, high phosphorus in molten steel, etc., to ensure smoothness and stability, reduce the burden of converter steelmaking, and make steel Efficiency effect
- Summary
- Abstract
- Description
- Claims
- Application Information
AI Technical Summary
Problems solved by technology
Method used
Image
Examples
Embodiment 1
[0030] Embodiment 1: The double smelting dephosphorization process of the present high-phosphorus molten iron adopts the following specific process.
[0031] Experiments were carried out in a 2t electric furnace: by adding iron ore, phosphorus ferroalloy and ferrosilicon alloy, phosphorus was configured to 0.73% for simulated hot metal pre-dephosphorization, using lime block, bauxite, concentrate powder, fluorite particles and fluorite powder , Lime powder is used as raw material for pre-dephosphorization operation. After the molten iron is melted in the electric furnace, desiliconization slagging material and dephosphorization slagging material are added respectively for slagging, the temperature of the molten iron is controlled at 1350-1400 ° C, the basicity of the initial slag is 1.0, and the basicity of the final slag is controlled at 1.9; The weight content of phosphorus slagging material components is: CaO 45%, SiO 2 20%, FeO 18%, Al 2 o 3 8%, CaF 5%, Na 2 O 4%. A...
Embodiment 2
[0032] Embodiment 2: The double smelting dephosphorization process of the high-phosphorus molten iron adopts the following specific process.
[0033]Experiments were carried out in a 2t electric furnace: by adding iron ore, phosphorus ferroalloy and ferrosilicon alloy, the phosphorus was configured to 0.95% for simulated hot metal pre-dephosphorization, using lime blocks, ferrite, concentrate powder, fluorite particles and fluorite powder , Lime powder is used as raw material for pre-dephosphorization operation. After the molten iron is melted in the electric furnace, desiliconization slagging material and dephosphorization slagging material slagging material are added respectively for slagging, the temperature of the molten iron is controlled at 1350-1400 ° C, the basicity of the initial slag is 1.1, and the basicity of the final slag is controlled at 2.0; The weight content of phosphorus slagging material composition is: CaO 42%, SiO 2 22%, FeO 20%, Al 2 o 3 5%, CaF 6%,...
Embodiment 3
[0034] Embodiment 3: The double smelting dephosphorization process of the high-phosphorus molten iron adopts the following specific process.
[0035] Experiment in 2t electric furnace: by adding iron ore, phosphorus ferroalloy and ferrosilicon alloy, phosphorus is configured to 0.57% for simulated hot metal pre-dephosphorization, using lime block, bauxite, concentrate powder, fluorite particles and fluorite powder , Lime powder is used as raw material for pre-dephosphorization operation. After the molten iron is melted in the electric furnace, desiliconization slagging material and dephosphorization slagging material slagging material are added respectively for slagging, the temperature of the molten iron is controlled at 1350-1400 °C, the basicity of the initial slag is 1.05, and the basicity of the final slag is controlled at 2.0; The weight content of phosphorus slagging material components is: CaO 40%, SiO 2 21%, FeO 19%, Al 2 o 3 10%, CaF 7%, Na 2 O 3%. After the d...
PUM
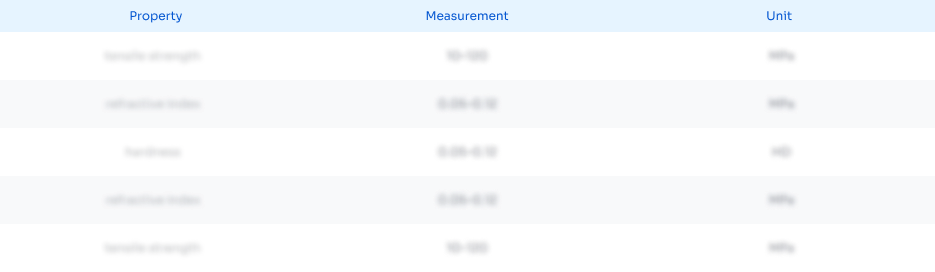
Abstract
Description
Claims
Application Information

- Generate Ideas
- Intellectual Property
- Life Sciences
- Materials
- Tech Scout
- Unparalleled Data Quality
- Higher Quality Content
- 60% Fewer Hallucinations
Browse by: Latest US Patents, China's latest patents, Technical Efficacy Thesaurus, Application Domain, Technology Topic, Popular Technical Reports.
© 2025 PatSnap. All rights reserved.Legal|Privacy policy|Modern Slavery Act Transparency Statement|Sitemap|About US| Contact US: help@patsnap.com