Process for recovering lithium phosphorous from lithium phosphate crude product to prepare battery-level lithium carbonate and iron phosphate
A lithium phosphate, battery-level technology, applied in the direction of lithium carbonate;/acid carbonate, phosphorus compounds, chemical instruments and methods, etc., can solve the problems of high impurities, high acid consumption, low value, etc., to achieve Improve economic value, increase recovery rate, and reduce emissions
- Summary
- Abstract
- Description
- Claims
- Application Information
AI Technical Summary
Problems solved by technology
Method used
Image
Examples
preparation example Construction
[0050] In the preparation process of battery-grade ferric orthophosphate in this step C, the reaction temperature is maintained at 80-95° C., and what is obtained at a low reaction temperature is amorphous ferric orthophosphate. The amorphous ferric orthophosphate has a fine particle size and a large specific surface area. Filtering, Difficult to wash, high residue of impurities, increasing the synthesis temperature, the amorphous ferric orthophosphate is transformed into crystalline ferric orthophosphate, which is easy to filter and wash. The chemical reaction equation involved in this step C is as follows:
[0051] Li 3 PO 4 (s)+2H + →LiH 2 PO 4 (l)+2Li +
[0052] LiH 2 PO4(1)→H 2 PO 4 - +Li +
[0053] h 2 PO 4 - →HPO 4 2- +H +
[0054] HPO 4 2- → PO 4 3- +H +
[0055] Fe 3+ +PO 4 3- +2H 2 O→FePO 4 2H 2 O(s)
[0056] D. Preparation of battery grade lithium carbonate
[0057] The lithium-containing mother liquor obtained above is filtered with...
example 1
[0073] This example reclaims lithium phosphorus from crude species to prepare battery-grade lithium carbonate and the specific process of iron phosphate as follows:
[0074] 1. Take 0.5kg of lithium phosphate and add 1.9kg of pure water. After 1 hour of high-speed dispersion and slurry mixing, the sand mill circulates sand for 0.5 hours to obtain lithium phosphate dispersion slurry.
[0075] 2. Take 1.05 kg of ferric sulfate and add water to prepare a solution with an iron content of 55 g / L, stir and dissolve, then filter to obtain a refined ferric sulfate solution.
[0076] 3. Add pure water into the reactor as the bottom liquid, add sulfuric acid to adjust the pH of the solution to 2, stir and heat up to 90°C, then add lithium phosphate slurry and ferric sulfate solution into the reactor simultaneously according to the reaction stoichiometric ratio for reaction. Maintain the reaction temperature at 90°C, control the addition of materials for 2 hours, and keep stirring for 2 ho...
example 2
[0081] This example reclaims lithium phosphorus from crude species to prepare battery-grade lithium carbonate and the specific process of iron phosphate as follows:
[0082] 1. After adding 0.5kg of lithium phosphate to 1.2kg of pure water, high-speed dispersion and slurry mixing for 0.5 hours, sand mill circulation for 1.0 hours to obtain lithium phosphate dispersion slurry.
[0083] 2. Take 1.05 kg of ferric sulfate and add water to prepare a solution with an iron content of 65 g / L. After stirring and dissolving, filter to obtain a refined ferric sulfate solution.
[0084] 3. Add washing water into the reactor as the bottom liquid, add sulfuric acid to adjust the pH of the solution to 2.5, stir and heat up to 85°C, then add lithium phosphate slurry and ferric sulfate solution into the reactor simultaneously according to the reaction stoichiometric ratio for reaction. Maintain the reaction temperature at 85°C, control the addition of materials for 2.5 hours, and keep stirring...
PUM
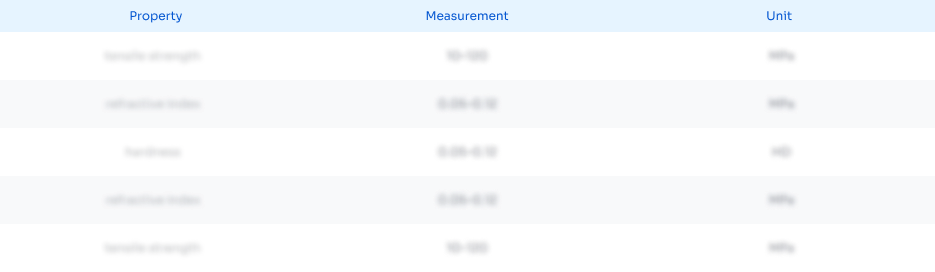
Abstract
Description
Claims
Application Information

- Generate Ideas
- Intellectual Property
- Life Sciences
- Materials
- Tech Scout
- Unparalleled Data Quality
- Higher Quality Content
- 60% Fewer Hallucinations
Browse by: Latest US Patents, China's latest patents, Technical Efficacy Thesaurus, Application Domain, Technology Topic, Popular Technical Reports.
© 2025 PatSnap. All rights reserved.Legal|Privacy policy|Modern Slavery Act Transparency Statement|Sitemap|About US| Contact US: help@patsnap.com