Method for machining inner spherical surface of bearing seat through movement forming
A technology of forming processing and bearing seat, which is applied in the direction of spherical grinding machine, grinding feed movement, metal processing equipment, etc., can solve the problems of small cutting force, high tool cost, low processing efficiency, etc., and achieve the improvement of dimensional accuracy and roughness , Reduce processing cost, high processing accuracy
- Summary
- Abstract
- Description
- Claims
- Application Information
AI Technical Summary
Problems solved by technology
Method used
Image
Examples
Embodiment Construction
[0037] In order to further explain the technical solution of the present invention, the present invention will be described in detail below through specific examples.
[0038] A method for processing the inner spherical surface of a bearing seat through motion forming, comprising the following steps:
[0039] (1) if figure 1 As shown, the bearing seat 1a is installed on the workpiece spindle 1 of the machine tool, the turning tool 21 is installed on the turning tool holder 2, and the diamond grinding wheel 31 is installed on the grinding head spindle 3. At this time, the workpiece spindle 1, the turning tool holder 2 and the grinding wheel The head spindles 3 are respectively located in their original positions, the workpiece spindle 1, the turning tool holder 2 and the grinding head spindle 3 are located on the same plane, and the extension line of the workpiece spindle 1 and the extension line of the grinding head spindle 3 intersect at one point, which is denoted as O poin...
PUM
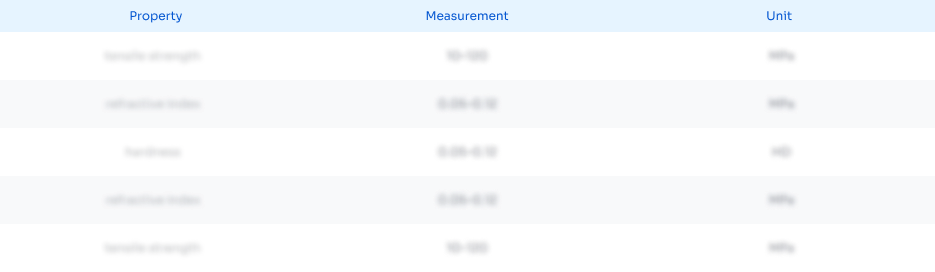
Abstract
Description
Claims
Application Information

- Generate Ideas
- Intellectual Property
- Life Sciences
- Materials
- Tech Scout
- Unparalleled Data Quality
- Higher Quality Content
- 60% Fewer Hallucinations
Browse by: Latest US Patents, China's latest patents, Technical Efficacy Thesaurus, Application Domain, Technology Topic, Popular Technical Reports.
© 2025 PatSnap. All rights reserved.Legal|Privacy policy|Modern Slavery Act Transparency Statement|Sitemap|About US| Contact US: help@patsnap.com