A forward drawing-backward bulging composite superplastic forming device and method thereof under the action of sheet material inflated back pressure
A technology for superplastic forming and sheet metal, which is applied in the field of superplastic forming devices and can solve the problems of unformable parts and broken parts walls.
- Summary
- Abstract
- Description
- Claims
- Application Information
AI Technical Summary
Problems solved by technology
Method used
Image
Examples
specific Embodiment approach 1
[0049] Specific implementation mode one: combine figure 1 Describe this embodiment. This embodiment is a forward drawing-backward bulging composite superplastic forming device under the action of sheet material inflation back pressure, including a punch 1, a pressure ring 2, a die 3 and an air hole 4;
[0050] The inside of the die 3 is provided with a die cavity 5 and an inflation hole 4, and the bottom of the die cavity 5 communicates with the inflation hole 4;
[0051] The top of the die 3 is provided with a punch 1 and a pressure ring 2; the punch 1 is placed inside the pressure ring 2, the central axis of the punch 1 and the die 3 coincides, and the punch 1 can be connected to the die cavity 5 Clamping;
[0052] The inner diameter of the pressure ring 2 is equal to the diameter of the inner wall cross-section at the top of the die cavity 5;
[0053] The plate to be formed is placed in the gap formed by the punch 1 , the pressure ring 2 and the die 3 .
specific Embodiment approach 2
[0054] Specific embodiment 2: In this embodiment, a forward drawing-backward bulging composite superplastic forming method under the action of sheet inflated back pressure is to use a forward drawing-backward bulging under the action of sheet inflated back pressure Shaped composite superplastic forming device is completed, specifically according to the following steps:
[0055] 1. Mold assembly: connect the punch 1 to the inner slider of the double-action press through the pressure plate, so that the punch 1 can move up and down; connect the pressure ring 2 to the outer slider of the double-action press through the pressure plate, so that The pressure ring 2 can move up and down; then the die 3 is fixed on the lower platform of the double-action press through the pressure plate;
[0056] 2. Heating: place the plate to be formed on the die 3, move the punch 1 and the pressure ring 2, so that the punch 1 and the pressure ring 2 are in contact with the plate to be formed; The te...
specific Embodiment approach 3
[0066] Embodiment 3: The difference between this embodiment and Embodiment 2 is that the plate to be formed in Step 2 is titanium alloy, aluminum alloy, magnesium alloy, superalloy or stainless steel. Others are the same as in the second embodiment.
PUM
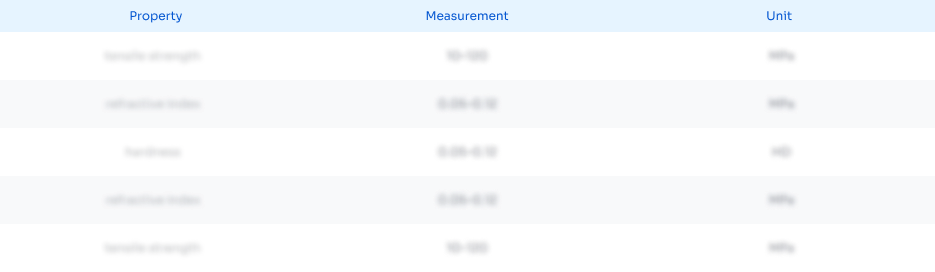
Abstract
Description
Claims
Application Information

- R&D
- Intellectual Property
- Life Sciences
- Materials
- Tech Scout
- Unparalleled Data Quality
- Higher Quality Content
- 60% Fewer Hallucinations
Browse by: Latest US Patents, China's latest patents, Technical Efficacy Thesaurus, Application Domain, Technology Topic, Popular Technical Reports.
© 2025 PatSnap. All rights reserved.Legal|Privacy policy|Modern Slavery Act Transparency Statement|Sitemap|About US| Contact US: help@patsnap.com