Method of rectifying and refining epoxypropane through reaction
A technology of propylene oxide and reactive distillation, applied in the direction of sustainable manufacturing/processing, chemical industry, climate sustainability, etc., can solve problems such as high energy consumption, achieve low equipment investment and operation energy consumption, high-efficiency removal, The effect of high process integration
- Summary
- Abstract
- Description
- Claims
- Application Information
AI Technical Summary
Problems solved by technology
Method used
Image
Examples
Embodiment 1
[0035] In the experiment, a small-scale rectification column with an inner diameter of 20mm, a height of 2500mm, and a 1.5x1.5mm triangular spiral packing was used, and the number of theoretical plates was about 65. The measured composition of crude PO raw materials in the experiment is shown in Table 3 below. The small test feed rate is 2ml / min, the feed position is 1000mm from the top of the tower, the top pressure is maintained at 160kPa, the reflux ratio is 2.5, and the recovery rate at the top of the tower is 0.992. The reaction entrainer is aniline, the molar ratio of it to the crude PO feed is 0.0015, and the feed position is 1550 mm from the top of the tower. Under this condition, the temperature of the tower bottom was 102° C., and the composition of the overhead liquid was shown in Table 3 below. Based on this calculation, the PO recovery rate in the small test experiment was 99.59%, and the total removal rate of aldehyde impurities was 63.90%, among which the remova...
Embodiment 2、3
[0040] Except for the reaction entrainer, other experimental conditions were the same as in Example 1. The reaction entrainer of embodiment 2,3 is respectively phenylhydrazine, semicarbazide, and experimental result is as shown in table 4, and small test experiment PO recovery rate is respectively 99.61%, 99.61%, and total aldehyde removal rate is respectively 82.35%, 81.08% %, the removal rates of formaldehyde were 99.25%, 99.16%, and the removal rates of propionaldehyde were 99.64%, 99.61%.
[0041] Table 4 Embodiment 2~5 overhead liquid composition
[0042]
Embodiment 4
[0044] The height of the experimental rectification tower is 1900 mm, the number of theoretical plates is about 50, the distance between the feed plate of crude PO and reaction entrainer is 750 mm and 1350 mm respectively from the top of the tower, and other conditions are the same as in Example 2. The experimental results of the overhead distillate composition are shown in Table 5 below. From this, the PO recovery rate of the small test experiment is calculated to be 99.57%, and the total removal rate of aldehyde impurities is 72.44%, wherein the formaldehyde removal rate is 98.28%, and the propionaldehyde removal rate is 99.57%. The removal rate is 98.80%.
[0045] Table 5 Example 4 overhead distillate composition
[0046]
PUM
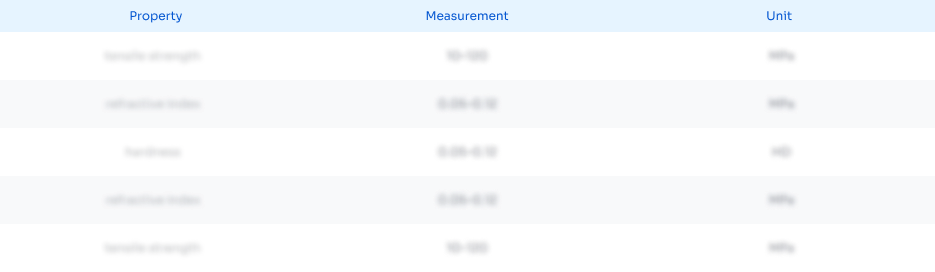
Abstract
Description
Claims
Application Information

- R&D
- Intellectual Property
- Life Sciences
- Materials
- Tech Scout
- Unparalleled Data Quality
- Higher Quality Content
- 60% Fewer Hallucinations
Browse by: Latest US Patents, China's latest patents, Technical Efficacy Thesaurus, Application Domain, Technology Topic, Popular Technical Reports.
© 2025 PatSnap. All rights reserved.Legal|Privacy policy|Modern Slavery Act Transparency Statement|Sitemap|About US| Contact US: help@patsnap.com