Catalyst and method for synthesizing polyethylene oxide polymer
A polyoxyethylene and synthesis method technology, applied in the chemical industry, can solve problems such as metal ion residues, polyoxyethylene polymer product quality and production environmental protection, and cannot be applied to industrial production fields, etc., to achieve strong catalytic activity and control Effects on production cost, quality improvement and environmental friendliness
- Summary
- Abstract
- Description
- Claims
- Application Information
AI Technical Summary
Problems solved by technology
Method used
Image
Examples
Embodiment 1
[0032] This embodiment provides a synthetic method for polyoxyethylene polymers, specifically comprising the following steps:
[0033] 1. Add 0.5 moles of methacryl alcohol to the high-pressure experimental reactor, and add 26.5 moles of ethylene oxide to the metering tank.
[0034] 2, continue to add the synthetic catalyst of polyoxyethylene polymer in reactor, the add-on of catalyst is 0.01% of methacryl alcohol and oxirane quality and, and catalyst is made of 18-crown (ether)-6, hydrogen Composition of Potassium Oxide and Methyltriphenylphosphine Bromide, wherein the number of moles of 18-crown (ether)-6: the number of moles of Potassium Hydroxide: the number of moles of Methyltriphenylphosphine Bromide=1:0.5:0.5 .
[0035] 3. After sealing the kettle, carry out nitrogen replacement, and the temperature inside the kettle rises to 100-120°C. At 100-120°C, start to add the ethylene oxide in the metering tank into the reaction kettle, and gradually raise the temperature, con...
Embodiment 2
[0039] This embodiment provides a synthetic method for polyoxyethylene polymers, specifically comprising the following steps:
[0040] 1. Add 0.5 moles of prenol to the high-pressure experimental reactor, and add 25 moles of ethylene oxide to the metering tank.
[0041] 2, continue to add the synthetic catalyst of polyoxyethylene polymer in reactor, the add-on of catalyzer is 0.1% of prenyl alcohol and oxirane quality and, and catalyzer is made of 15-crown (ether)-5, hydrogenation Composition of sodium and ethyltriphenylphosphine bromide, wherein the number of moles of 15-crown (ether)-5: the number of moles of sodium hydride: the number of moles of ethyltriphenylphosphine bromide=1:0.8:0.6.
[0042] 3. After sealing the kettle, carry out nitrogen replacement, and the temperature inside the kettle rises to 100-120°C. At 100-120°C, start to add the ethylene oxide in the metering tank into the reaction kettle, and gradually raise the temperature, control the reaction temperatur...
Embodiment 3
[0046] This embodiment provides a synthetic method for polyoxyethylene polymers, specifically comprising the following steps:
[0047] 1. Add 0.5 moles of 1,4-butenediol to the high-pressure experimental reactor, and add 32 moles of ethylene oxide to the metering tank.
[0048] 2. Continue to add the synthesis catalyst of polyoxyethylene polymer in the reactor, the addition of catalyst is 0.3% of the mass sum of 1,4-butene diol and ethylene oxide, and the catalyst consists of 12-crown (ether) -4. Lithium metal and propyl triphenylphosphine bromide, wherein the number of moles of 12-crown (ether)-4: the number of moles of lithium metal: the number of moles of propyl triphenylphosphine bromide=1:1.1 :0.5.
[0049] 3. After sealing the kettle, carry out nitrogen replacement, and the temperature inside the kettle rises to 100-120°C. At 100-120°C, start to add the ethylene oxide in the metering tank into the reaction kettle, and gradually raise the temperature, control the reaction...
PUM
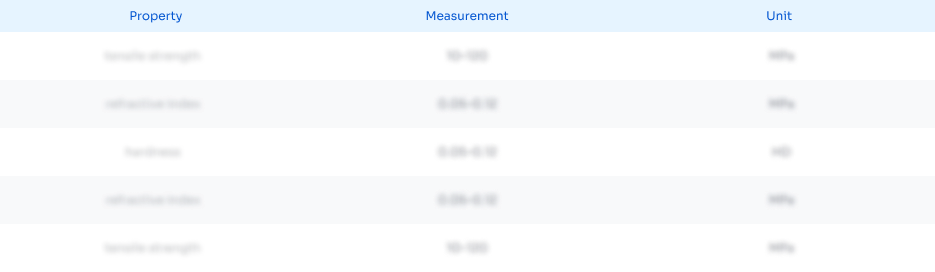
Abstract
Description
Claims
Application Information

- R&D
- Intellectual Property
- Life Sciences
- Materials
- Tech Scout
- Unparalleled Data Quality
- Higher Quality Content
- 60% Fewer Hallucinations
Browse by: Latest US Patents, China's latest patents, Technical Efficacy Thesaurus, Application Domain, Technology Topic, Popular Technical Reports.
© 2025 PatSnap. All rights reserved.Legal|Privacy policy|Modern Slavery Act Transparency Statement|Sitemap|About US| Contact US: help@patsnap.com