Rolling method and device for headless continuous casted and rolled ultra-low carbon steel roll ferrite used for ultra-deep drawing
An ultra-low carbon steel, continuous casting and rolling technology, applied in metal rolling, metal rolling, manufacturing tools, etc., can solve the problems of stable performance control, complicated process, low production efficiency, etc., and eliminate adverse effects , reduce costs and improve efficiency
- Summary
- Abstract
- Description
- Claims
- Application Information
AI Technical Summary
Problems solved by technology
Method used
Image
Examples
Embodiment 1
[0042] According to the chemical composition and mass percentage of ultra-low carbon steel: C: 0.007%, Si: 0.05%, Mn: 0.25%, Nb: 0.003%, Ti: 0.070%, Als: 0.045%, P: 0.015%, S : 0.010%, N: 0.005%, O: 0.0035%, and the rest is Fe and unavoidable impurities for smelting. The slab is cast in a continuous casting machine, the temperature of the continuous casting ladle is 1560°C, the casting speed is 4m / min, and the thickness of the slab is 130mm. It is directly sent to the rough rolling unit for rough rolling. The rough rolling temperature is 1100°C-1050°C. After rough rolling, the thickness of the intermediate billet is 25mm. The intermediate billet enters the cooling channel to control the temperature, the cooling speed is 38°C / s, the rolling shear head is descaled by high-pressure water, the descaling water pressure is 30MPa, the finishing rolling unit is finishing rolling, the purge water between the stands is put into use, and the finishing rolling temperature Controlled at 8...
Embodiment 2
[0044]According to the chemical composition and mass percentage of ultra-low carbon steel: C: 0.005%, Si: 0.03%, Mn: 0.18%, Nb: 0.020%, Ti: 0.050%, Als: 0.060%, P: 0.010%, S : 0.008%, N: 0.004%, O: 0.0030%, and the rest is Fe and unavoidable impurities for smelting. The slab is cast in a continuous casting machine, the temperature of the continuous casting ladle is 1563°C, the casting speed is 5m / min, and the thickness of the slab is 110mm. It is directly sent to the rough rolling unit for rough rolling. The rough rolling temperature is 1110°C-1060°C. After rough rolling, the thickness of the intermediate billet is 18mm. The intermediate billet enters the cooling channel to control the temperature, the cooling speed is 27℃ / s, the rolling shear head is descaled by high-pressure water, the descaling water pressure is 28MPa, the finishing rolling unit is finishing rolling, the purge water between the stands is put into use, and the finishing rolling temperature Controlled at 830...
Embodiment 3
[0046] According to the chemical composition and mass percentage of ultra-low carbon steel: C: 0.003%, Si: 0.02%, Mn: 0.12%, Nb: 0.035%, Ti: 0.030%, Als: 0.025%, P: 0.012%, S : 0.005%, N: 0.0035%, O: 0.0020%, and the rest is Fe and unavoidable impurities for smelting. The slab is cast in a continuous casting machine, the temperature of the continuous casting ladle is 1570°C, the casting speed is 6m / min, and the thickness of the slab is 90mm. It is directly sent to the rough rolling unit for rough rolling. The rough rolling temperature is 1130°C-1070°C. After rough rolling, the thickness of the intermediate billet is 11mm. The intermediate billet enters the cooling channel to control the temperature, the cooling speed is 15°C / s, the rolling shear head is descaled by high-pressure water, the descaling water pressure is 30MPa, the finishing rolling unit is finishing rolling, the purge water between the stands is put into use, and the finishing rolling temperature Controlled at 8...
PUM
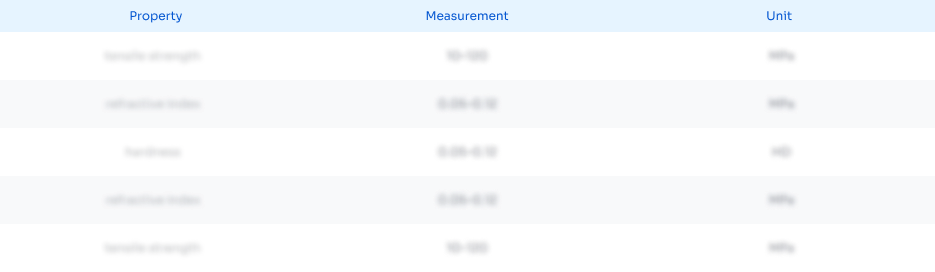
Abstract
Description
Claims
Application Information

- Generate Ideas
- Intellectual Property
- Life Sciences
- Materials
- Tech Scout
- Unparalleled Data Quality
- Higher Quality Content
- 60% Fewer Hallucinations
Browse by: Latest US Patents, China's latest patents, Technical Efficacy Thesaurus, Application Domain, Technology Topic, Popular Technical Reports.
© 2025 PatSnap. All rights reserved.Legal|Privacy policy|Modern Slavery Act Transparency Statement|Sitemap|About US| Contact US: help@patsnap.com