Method for short-flow recovery of platinum group metal from waste catalysts
A technology of spent catalysts and platinum group metals, which is applied in the field of secondary resource recovery of precious metals, can solve the problems of difficult filtration, low yield, and high temperature of pyromelting, and achieve the effects of shortening the recovery process, high purity, and high refining efficiency
- Summary
- Abstract
- Description
- Claims
- Application Information
AI Technical Summary
Problems solved by technology
Method used
Image
Examples
Embodiment 1
[0017] Take 50g of spent catalyst (in which the platinum content is 1981g / t and the alumina is 76.2%). The waste catalyst was placed in a muffle furnace, calcined in two steps, and the temperature was controlled by program. The first step was kept at 700 ° C for 30 minutes, and the organic impurities were removed by burning. The second step was calcined at 1300 ° C for 30 minutes, and the γ- Al 2 O 3 Converted to α-Al 2 O 3 ; Cool to room temperature, place the calcined waste catalyst in a 500 mL beaker, add 200 mL of aqua regia with a mass concentration of 30% to dissolve the leached platinum, heat to 90 °C and stir for 1 h; after the reaction is complete, filter to obtain the leaching residue and the leaching solution, the leaching slag was used to recover alumina, the leaching solution was concentrated and acid-driven, the platinum content was 6.21g / L, the aluminum content was 0.0002g / L, the pH was adjusted to 7.0, and hydrazine hydrate was used for selective reduction, ...
Embodiment 2
[0019] Take 50g of spent catalyst (in which the platinum content is 1981g / t and the alumina is 76.2%). The waste catalyst was placed in a muffle furnace, calcined in two steps, and the temperature was controlled by program. The first step was kept at 800 °C for 30 minutes, and the organic impurities were removed by burning. The second step was calcined at 1300 °C for 35 minutes, and the γ- Al 2 O 3 Converted to α-Al 2 O 3 ; Cool to room temperature, place the calcined waste catalyst in a 500mL beaker, add 200ml of aqua regia with a mass concentration of 30% to dissolve the leached platinum, heat to 85 °C and stir for 1.5h; after the reaction is complete, filter to obtain the leaching The slag and leaching solution, the leaching slag was recovered alumina, the leaching solution was concentrated and acid-driven, the platinum content was 6.05g / L, the aluminum content was 0.0002g / L, the pH was adjusted to 7.0, and the hydrazine hydrate was selectively reduced to measure the alu...
Embodiment 3
[0021] Take 100g of spent catalyst (in which the platinum content is 1981g / t and the alumina is 76.2%). The waste catalyst was placed in a muffle furnace, calcined in two steps, and the temperature was controlled by program. The first step was kept at 750 °C for 30 minutes, and the organic impurities were removed by burning. The second step was calcined at 1300 °C for 40 minutes, and the γ- Al 2 O 3 Converted to α-Al 2 O 3 ; Cool to room temperature, place the calcined waste catalyst in a 1000mL beaker, add 400ml of aqua regia with a mass concentration of 30% to dissolve the leached platinum, heat to 80 °C and stir for 2h; after the reaction is complete, filter to obtain the leaching residue and the leaching solution, the leaching slag was used to recover alumina, the leaching solution was concentrated and the content of platinum was 6.50g / L, the content of aluminum was 0.0003g / L, the pH was adjusted to 8.0, and it was selectively reduced with hydrazine hydrate, and the con...
PUM
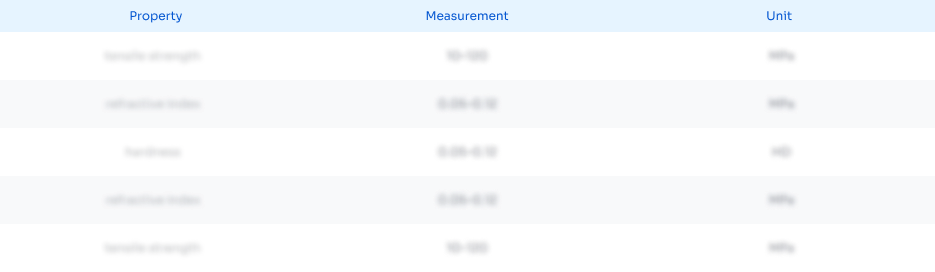
Abstract
Description
Claims
Application Information

- R&D Engineer
- R&D Manager
- IP Professional
- Industry Leading Data Capabilities
- Powerful AI technology
- Patent DNA Extraction
Browse by: Latest US Patents, China's latest patents, Technical Efficacy Thesaurus, Application Domain, Technology Topic, Popular Technical Reports.
© 2024 PatSnap. All rights reserved.Legal|Privacy policy|Modern Slavery Act Transparency Statement|Sitemap|About US| Contact US: help@patsnap.com