Aluminum-chromium alloy casting technology
A casting process and chromium alloy technology, which is applied in the field of aluminum-chromium alloy casting process, can solve the problems of low strength, coarse grain size, shrinkage cavity and shrinkage, etc., and achieve high strength, good machinability and low filling pressure Effect
- Summary
- Abstract
- Description
- Claims
- Application Information
AI Technical Summary
Problems solved by technology
Method used
Examples
Embodiment 1
[0013] An aluminum-chromium alloy casting process, in thermal solid solution treatment: the furnace loading temperature is 200°C, the heating rate is 110°C / hour, when the temperature rises to 700°C, heat preservation is carried out, and the heat preservation time is 1.5 hours. Heating at a speed of ℃ / hour to a molten liquid state, the annealing conditions are: keep warm at 850°C for 2.0 hours, then keep warm at 750°C for 4 hours, the quenching and tempering conditions are: keep warm at 1050°C for half an hour, air cooling, in Temper at 500°C for 2 hours.
[0014] As a further improvement to the above scheme, the chemical composition of the aluminum-chromium alloy contains the following components in terms of mass percentage: chromium accounts for 14%, silicon accounts for 8.5%, iron accounts for 0.8%, copper accounts for 0.4%, manganese accounts for 0.2%, Magnesium accounts for 0.5%, nickel accounts for 0.4%, zinc accounts for 0.2%, lead accounts for 0.08%, tin accounts for 0....
Embodiment 2
[0018] An aluminum-chromium alloy casting process, in thermal solid solution treatment: the furnace loading temperature is 210°C, the heating rate is 115°C / hour, when the temperature rises to 750°C, heat preservation is carried out, and the heat preservation time is 2.0 hours. Heating at a speed of ℃ / hour to a molten liquid state, the annealing conditions are: keep at 880°C for 2.2 hours, then keep at 800°C for 4.5 hours, the quenching and tempering conditions are: keep at 1080°C for half an hour, air cooling, in Temper at 530°C for 2.5 hours.
[0019] As a further improvement to the above scheme, the chemical composition of the aluminum-chromium alloy contains the following components in terms of mass percentage: chromium accounts for 15%, silicon accounts for 9.0%, iron accounts for 0.85%, copper accounts for 0.5%, manganese accounts for 0.25%, Magnesium accounts for 0.55%, nickel accounts for 0.45%, zinc accounts for 0.25%, lead accounts for 0.09%, tin accounts for 0.06%, a...
Embodiment 3
[0023] An aluminum-chromium alloy casting process, in thermal solution treatment: the furnace loading temperature is 230°C, the heating rate is 120°C / hour, when the temperature rises to 800°C, heat preservation is carried out, and the heat preservation time is 2.5 hours. Heating at a speed of ℃ / hour to a molten liquid state, the annealing conditions are: heat preservation at 900°C for 2.5 hours, and then heat preservation at 850°C for 5 hours, the quenching and tempering conditions are: heat preservation at 1100°C for half an hour, air cooling, in Temper at 550°C for 3 hours.
[0024] As a further improvement to the above scheme, the chemical composition of the aluminum-chromium alloy contains the following components in terms of mass percentage: chromium accounts for 16%, silicon accounts for 9.5%, iron accounts for 0.9%, copper accounts for 0.6%, manganese accounts for 0.3%, Magnesium accounts for 0.6%, nickel accounts for 0.5%, zinc accounts for 0.3%, lead accounts for 0.10...
PUM
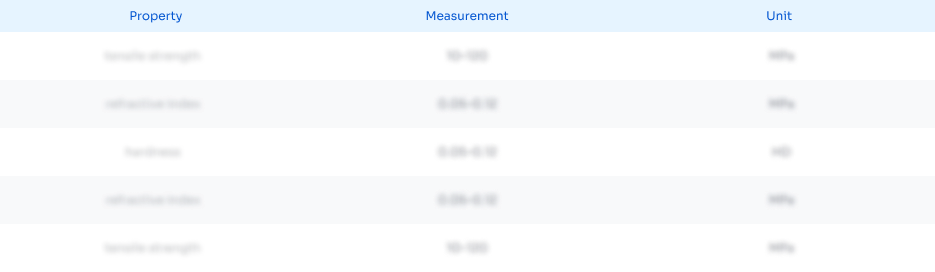
Abstract
Description
Claims
Application Information

- R&D Engineer
- R&D Manager
- IP Professional
- Industry Leading Data Capabilities
- Powerful AI technology
- Patent DNA Extraction
Browse by: Latest US Patents, China's latest patents, Technical Efficacy Thesaurus, Application Domain, Technology Topic, Popular Technical Reports.
© 2024 PatSnap. All rights reserved.Legal|Privacy policy|Modern Slavery Act Transparency Statement|Sitemap|About US| Contact US: help@patsnap.com