Full-steel-scrap electric arc furnace cleanness rapid smelting method
A smelting method and electric arc furnace technology, applied in the field of electric arc furnace steelmaking, can solve the problems of small number of CO bubbles, low carbon content in molten pool, insufficient oxygen supply intensity, etc.
- Summary
- Abstract
- Description
- Claims
- Application Information
AI Technical Summary
Problems solved by technology
Method used
Image
Examples
Embodiment 1
[0027] Embodiment 1: The present invention is applied in 90t electric arc furnace steelmaking. Two spray guns are installed, distributed on both sides of the electric arc furnace door. The inner diameter of the spray guns is 12 mm, and the annular gap is 1 mm. They are made of stainless steel. The outlet of the spray gun is 800mm below the liquid steel surface, and the angle with the horizontal plane is 15°. The decarburization powder is graphite recarburizer, the dephosphorization powder is lime powder, the particle diameter is 50μm, and the single-gun powder spraying rate is 0-100kg / min. Carrier gas A is air, carrier gas B is oxygen, and the oxygen flow rate of a single gun is 50-800Nm 3 / h. Gap gas is N 2 , Ar or natural gas, the flow rate of a single gun is 10-200Nm 3 / h. Spray gun injection process see image 3 .
[0028] 1) After tapping the electric arc furnace and before adding the furnace charge, use the dephosphorization conveying pipeline to spray, spray the c...
Embodiment 2
[0040] Embodiment 2: The present invention is applied in 150t electric arc furnace steelmaking. Four spray guns are installed, which are evenly distributed on both sides of the electric arc furnace door. The outlet of the spray gun is 900mm below the liquid steel surface, and the angle with the horizontal plane is 10°. The decarbonization powder is carbon powder, the dephosphorization powder is lime powder, the particle diameter is 30μm, and the single-gun powder spraying rate is 0-50kg / min. Carrier gas A is N 2 , the carrier gas B is O 2 -CO 2 Mixed gas, single gun oxygen flow 50~600Nm 3 / h. Gap gas is N 2 , Ar or propane, the single gun flow rate is 10-200Nm 3 / h.
[0041] 1) After tapping the electric arc furnace and before adding the furnace charge, use the dephosphorization conveying pipeline to spray, spray the central pipe of the spray gun and the annular seam pipe to spray N 2 , the central tube flow rate is 100Nm 3 / h, the flow rate of the circular seam pipe ...
PUM
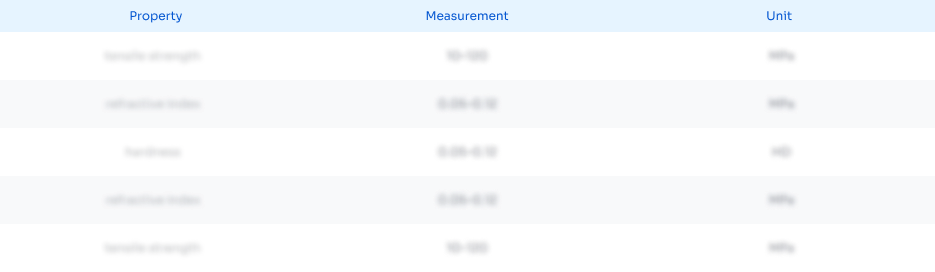
Abstract
Description
Claims
Application Information

- R&D
- Intellectual Property
- Life Sciences
- Materials
- Tech Scout
- Unparalleled Data Quality
- Higher Quality Content
- 60% Fewer Hallucinations
Browse by: Latest US Patents, China's latest patents, Technical Efficacy Thesaurus, Application Domain, Technology Topic, Popular Technical Reports.
© 2025 PatSnap. All rights reserved.Legal|Privacy policy|Modern Slavery Act Transparency Statement|Sitemap|About US| Contact US: help@patsnap.com