Process method of trench type dual-layer-gate MOS dielectric layer
A process method and dielectric layer technology, applied in electrical components, semiconductor/solid-state device manufacturing, semiconductor devices, etc., can solve the problems of easy breakdown of gate polysilicon and low yield, improve gate/source leakage, optimize film texture, the effect of increasing thickness
- Summary
- Abstract
- Description
- Claims
- Application Information
AI Technical Summary
Problems solved by technology
Method used
Image
Examples
Embodiment Construction
[0021] The process method of the trench-type double-layer gate MOS dielectric layer according to the present invention comprises:
[0022] Step 1, such as figure 2 As shown, a groove is formed by etching on the silicon substrate, and a dielectric layer 1 is grown inside the groove. The dielectric layer includes a thermal oxide layer and a composite liner film layer of oxide film / nitride film / oxide film; or thermal oxidation Add a nitride film layer; and fill the trench with polysilicon 2 for the first time, etch back the polysilicon and the dielectric layer, leaving the upper half of the trench free, and the remaining polysilicon at the bottom as the source.
[0023] The second step is to perform thermal oxidation to form a thermal oxide layer 3 and deposit a high-density plasma oxide film 4; then perform a second polysilicon deposition 5 to fill the trench, and then perform polysilicon etching back, that is, etching back to the trench The polysilicon in the groove is flush ...
PUM
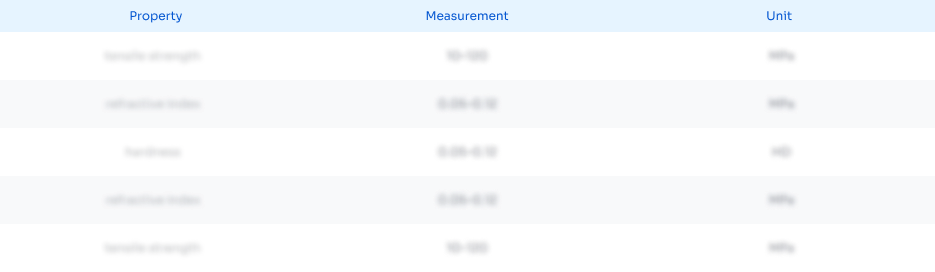
Abstract
Description
Claims
Application Information

- R&D Engineer
- R&D Manager
- IP Professional
- Industry Leading Data Capabilities
- Powerful AI technology
- Patent DNA Extraction
Browse by: Latest US Patents, China's latest patents, Technical Efficacy Thesaurus, Application Domain, Technology Topic, Popular Technical Reports.
© 2024 PatSnap. All rights reserved.Legal|Privacy policy|Modern Slavery Act Transparency Statement|Sitemap|About US| Contact US: help@patsnap.com