Novel process for recovering metallic rhenium from copper smelting waste acid
A copper smelting and new process technology, applied in the new process field of metal rhenium recovery, can solve the problems of low recovery rate of valence metals, high investment cost, complex process, etc., and achieve large processing capacity, low investment cost, and short process flow Effect
- Summary
- Abstract
- Description
- Claims
- Application Information
AI Technical Summary
Problems solved by technology
Method used
Image
Examples
Embodiment 1
[0024] (1) Raw material pretreatment process: the solid particles in copper smelting waste acid are removed by one-stage plate and frame filter press and two-stage drum expansion filter to obtain copper smelting waste acid clear liquid;
[0025](2) Centrifugal extraction process: Prepare and group 7.5% N235 + 40% 2-octanol + 260# solvent oil mixed organic phase 20L as the extraction agent, through the flow meter according to the ratio O / A=1 / 10, control the entry The waste acid of the centrifugal extraction separator is 15L / h and the feed rate of the extractant is 1.5L / h. Three-stage countercurrent extraction is adopted, and the single-stage centrifugal extraction time is 4s to obtain a rhenium-containing loaded organic phase and an oil-containing raffinate, containing The rhenium-loaded organic phase is sent to the centrifugal washing process, and the oily raffinate is sent to the sewage acid treatment process of the copper smelter after degreasing, and the organic phase is ret...
Embodiment 2
[0032] (1) Raw material pretreatment process: the copper smelting waste acid is vacuum filtered with a filter cloth of 2000 mesh to remove solid particles in the copper smelting waste acid to obtain a copper smelting waste acid clear liquid;
[0033] (2) Centrifugal extraction process: prepare a mixed organic phase of 7.5% N235 + 40% 2-octanol + 260# solvent oil 2m 3 As an extractant, the processing capacity of waste acid from copper smelting is 600L / h, and the amount of waste acid from copper smelting and extractant entering the centrifuge extraction separator is controlled by a flow meter according to the ratio O / A=1 / 10, using 3 Stage countercurrent extraction, single-stage centrifugal extraction time is 4s, to obtain rhenium-containing organic phase and oil-containing raffinate, rhenium-containing organic phase is sent to centrifugal washing process, and oil-containing raffinate is sent to copper smelter for sewage acid treatment after degreasing process, the organic phase ...
Embodiment 3
[0041] (1) Raw material pretreatment process: the solid particles in copper smelting waste acid are removed by one-stage plate and frame filter press and two-stage drum expansion filter to obtain copper smelting waste acid clear liquid;
[0042] (2) Centrifugal extraction process: prepare a mixed organic phase of 7.5% N235 + 40% 2-octanol + 260# solvent oil 2m 3 As an extraction agent, the processing capacity of waste acid from copper smelting is 800L / h, and the amount of waste acid from copper smelting and extraction agent entering the centrifugal extraction separator is controlled by a flow meter according to O / A=1 / 10, using 3 Stage countercurrent extraction, single-stage centrifugal extraction time is 4s, get rhenium-containing organic phase and oil-containing raffinate, rhenium-containing organic phase is sent to centrifugal washing process, oil-containing raffinate is sent to raffinate oil separation tank to remove organic phase Finally, it is sent to the copper smelter s...
PUM
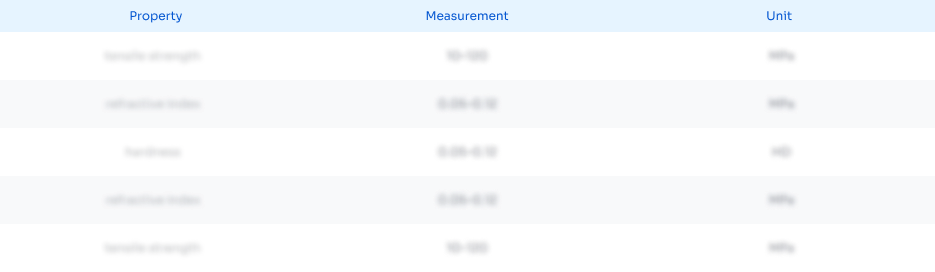
Abstract
Description
Claims
Application Information

- Generate Ideas
- Intellectual Property
- Life Sciences
- Materials
- Tech Scout
- Unparalleled Data Quality
- Higher Quality Content
- 60% Fewer Hallucinations
Browse by: Latest US Patents, China's latest patents, Technical Efficacy Thesaurus, Application Domain, Technology Topic, Popular Technical Reports.
© 2025 PatSnap. All rights reserved.Legal|Privacy policy|Modern Slavery Act Transparency Statement|Sitemap|About US| Contact US: help@patsnap.com