Method for preparing corrosion-resistant anti-channeling agent for oil well cement
A technology of oil well cement and anti-channeling agent, applied in the field of cement, can solve the problems of low strength, no anti-corrosion properties, no high strength, etc., and achieve the effects of good compressive strength, delaying thickening time and easy operation.
- Summary
- Abstract
- Description
- Claims
- Application Information
AI Technical Summary
Problems solved by technology
Method used
Examples
Embodiment
[0019] The present invention prepares the preparation method of anti-corrosion oil well cement anti-channeling agent, comprises the following steps:
[0020] (1) Calcium formate, sodium aluminate, mica, and kaolinite are crushed respectively, and then added in a grinder in proportion to grinding;
[0021] (2) Send the ground powder into the kiln, calcine at 1200-1800°C for 15-30 hours, and obtain clinker after cooling;
[0022] (3) Add styrene-butadiene rubber emulsion, butadiene-styrene, phosphate, sulfonate, and defoamer to the clinker, calcinate at 50-100°C for 15 minutes, and cool to room temperature;
[0023] (4) Add slag in proportion to step (3), mix evenly, and grind to a fineness of 400-500 mesh to obtain an oil well cement expansion agent.
[0024] in. Grind to a fineness of 450 mesh in the step (1). The calcination temperature in the kiln in the step (2) is 1590°C. The calcination time in the kiln in the step (2) is 26 hours. The calcining temperature in the st...
PUM
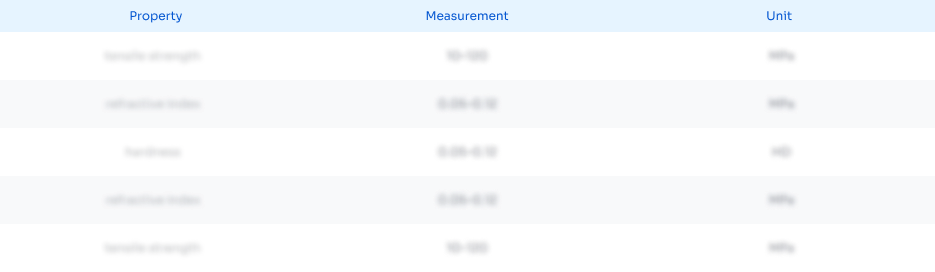
Abstract
Description
Claims
Application Information

- R&D
- Intellectual Property
- Life Sciences
- Materials
- Tech Scout
- Unparalleled Data Quality
- Higher Quality Content
- 60% Fewer Hallucinations
Browse by: Latest US Patents, China's latest patents, Technical Efficacy Thesaurus, Application Domain, Technology Topic, Popular Technical Reports.
© 2025 PatSnap. All rights reserved.Legal|Privacy policy|Modern Slavery Act Transparency Statement|Sitemap|About US| Contact US: help@patsnap.com