Process and system for recovering zinc via synergistic treatment with zinc-containing waste paint slag and distillers' grains
A technology for co-processing and waste paint, applied in the petroleum industry, process efficiency improvement, special form of dry distillation, etc., can solve problems such as large environmental impact, avoid high-temperature corrosion, improve adaptability, and prolong service life.
- Summary
- Abstract
- Description
- Claims
- Application Information
AI Technical Summary
Problems solved by technology
Method used
Image
Examples
Embodiment 1
[0058] After using a separate feed such as Figure 4 , Figure 5 In the layered distribution method shown, distiller's grains and zinc-containing waste paint slag are transported to the rotary bed pyrolysis device by separate pipelines for pyrolysis, and the pyrolysis temperature control in the rotary bed pyrolysis device adopts a partition control method. The temperature of each interval is 450°C in zone I, 450°C in zone II, 500°C in zone II, 650°C in zone III, 700°C in zone IV, and 700°C in zone IV. The total pyrolysis time is controlled at 80 minutes.
[0059] The mixed material passes through the above four sections sequentially in the rotary bed pyrolysis device, and then completes the process of drying, cracking and coordinated thermal cracking. The organic matter in distiller's grains and zinc-containing waste paint slag is cracked into small molecule combustible gas, tar, water vapor, and pyrolytic carbon under high-temperature and anaerobic conditions. Among them, th...
Embodiment 2
[0067] use Image 6 In the distribution method shown, the distiller's grains and zinc-containing waste paint slag are pre-mixed and stirred before being put into the furnace, and then sent to the rotary bed pyrolysis device by the common conveying pipeline. Complete and uniform mixing in the pyrolysis device. The pyrolysis temperature control in the rotary bed pyrolysis device adopts the zone control method, the temperature of the four zones are respectively 400°C in zone Ⅰ, 500°C in zone Ⅱ, 600°C in zone Ⅲ, 600°C in zone 4, and 700°C in zone Ⅳ. , the total pyrolysis time is controlled at 80min.
[0068] Subsequent steps are processed in the same manner as in the previous example to obtain the following specific experimental data and illustrate the advantages of mixed pyrolysis.
[0069] When distiller's grains are pyrolyzed alone, the heat value of pyrolysis gas is 3439kcal / m 3 , when zinc-containing waste paint slag is pyrolyzed separately, the heat value of pyrolysis gas...
Embodiment 3
[0072] A zinc-containing waste paint slag and distiller's grains co-processing zinc recovery process, which includes:
[0073] 1) The distiller's grains and zinc-containing waste paint slag are transported to the rotating bed pyrolysis device through a separate pipeline for such Figure 4 The way shown is cloth, and after the cloth is pyrolyzed, the pyrolysis temperature control in the rotary bed pyrolysis device adopts a partition control method, and the temperatures in the four intervals are 300°C in zone Ⅰ, 300°C in zone Ⅱ, 450°C in zone 3, and 450°C in zone Ⅲ. 4 The temperature is 550°C, the temperature in Zone Ⅳ 5 is 650°C, and the total pyrolysis time is controlled at 60min. The mixed material passes through the above four sections sequentially in the rotary bed pyrolysis device, and then completes the process of drying, cracking and coordinated thermal cracking. The metal zinc reduced in zone IV of the furnace will not be discharged into the rotary bed pyrolysis device...
PUM
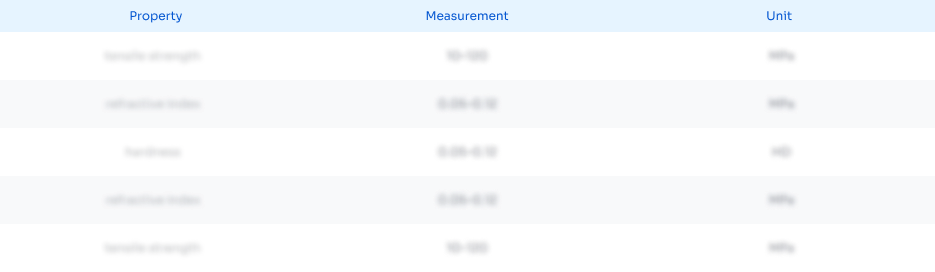
Abstract
Description
Claims
Application Information

- Generate Ideas
- Intellectual Property
- Life Sciences
- Materials
- Tech Scout
- Unparalleled Data Quality
- Higher Quality Content
- 60% Fewer Hallucinations
Browse by: Latest US Patents, China's latest patents, Technical Efficacy Thesaurus, Application Domain, Technology Topic, Popular Technical Reports.
© 2025 PatSnap. All rights reserved.Legal|Privacy policy|Modern Slavery Act Transparency Statement|Sitemap|About US| Contact US: help@patsnap.com