Technology and system for synergistically processing zinc-containing waste paint slag and vinasse and recovering zinc
A technology of co-processing and waste paint, which is applied in the direction of gasification process, petroleum industry, process efficiency improvement, etc., can solve the problems of large environmental impact, improve thermal efficiency, solve the problem of low calorific value of pyrolysis gas, and improve adaptability Effect
- Summary
- Abstract
- Description
- Claims
- Application Information
AI Technical Summary
Problems solved by technology
Method used
Image
Examples
Embodiment 1
[0058] After using a separate feed such as Figure 4 , Figure 5 In the layered distribution method shown, distiller's grains and zinc-containing waste paint slag are transported to the rotary bed pyrolysis device by separate pipelines for pyrolysis, and the pyrolysis temperature control in the rotary bed pyrolysis device adopts a partition control method. The temperature of each interval is 700°C in zone 2, 800°C in zone 2, 900°C in zone 3, 1000°C in zone 4, and 1000°C in zone 4. The total pyrolysis time is controlled at 80 minutes.
[0059] The mixed material passes through the above four sections sequentially in the rotary bed pyrolysis device, and then completes the process of drying, cracking and coordinated thermal cracking. The organic matter in distiller's grains and zinc-containing waste paint slag is cracked into small molecule combustible gas, tar and water vapor under high temperature and anaerobic conditions. Among them, the metal oxide of zinc-containing waste p...
Embodiment 2
[0063] use Image 6 In the distribution method shown, the distiller's grains and zinc-containing waste paint slag are pre-mixed and stirred before being put into the furnace, and then sent to the rotary bed pyrolysis device by the common conveying pipeline. Complete and uniform mixing in the pyrolysis device. The pyrolysis temperature control in the rotary bed pyrolysis device adopts the zone control method, and the temperature of the four zones are respectively 700°C in zone Ⅰ, 800°C in zone Ⅱ, 800°C in zone 3, 900°C in zone Ⅲ, and 1000°C in zone Ⅳ. , the total pyrolysis time is controlled at 80min. Subsequent steps are processed in the same manner as in the previous embodiment to obtain Image 6 The zinc oxide recovery rate of the material distribution method is 99.9%, and the heat input of the direct-fired boiler accounts for 73% of the heat of the dry material.
Embodiment 3
[0065] A zinc-containing waste paint slag and distiller's grains co-processing zinc recovery process, which includes:
[0066] 1) Distiller's grains and zinc-containing waste paint slag are transported to the rotary bed pyrolysis device by a separate pipeline for distribution. The distribution method is that the distiller's grains 7 are on the top and the zinc-containing waste paint residue 8 is on the bottom. After the distribution, it is pyrolyzed and rotated. The pyrolysis temperature control in the bed pyrolysis device adopts the partition control method. The temperature of the four intervals is 600 °C in area Ⅰ, 750 °C in area Ⅱ, 850 °C in area Ⅲ, 950 °C in area Ⅳ, and 950 °C in area Ⅳ. The total solution time was controlled within 60 minutes. The mixed material passes through the above four sections sequentially in the rotary bed pyrolysis device, and then completes the process of drying, cracking and coordinated thermal cracking. In zone IV of the furnace, all the meta...
PUM
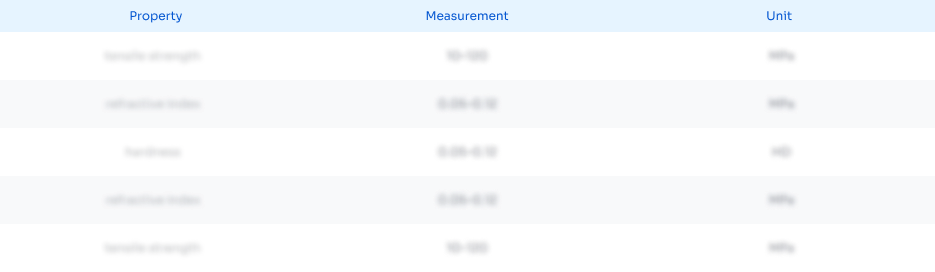
Abstract
Description
Claims
Application Information

- Generate Ideas
- Intellectual Property
- Life Sciences
- Materials
- Tech Scout
- Unparalleled Data Quality
- Higher Quality Content
- 60% Fewer Hallucinations
Browse by: Latest US Patents, China's latest patents, Technical Efficacy Thesaurus, Application Domain, Technology Topic, Popular Technical Reports.
© 2025 PatSnap. All rights reserved.Legal|Privacy policy|Modern Slavery Act Transparency Statement|Sitemap|About US| Contact US: help@patsnap.com