A kind of manufacturing method of bead wire
A production method and bead steel wire technology are applied in the field of steel wire production, which can solve the problems of reduced tire nipple tightening force, hidden danger of tire safety, weakened steel ring bearing capacity, etc. the effect of elimination
- Summary
- Abstract
- Description
- Claims
- Application Information
AI Technical Summary
Problems solved by technology
Method used
Examples
Embodiment 1
[0043] A method for manufacturing a bead wire, comprising the following steps:
[0044] Step 1. Laying out
[0045] Check the steel number and specification of the incoming material; push the pre-prepared semi-finished wheel into the pay-off machine, press the "jacking" button to push the thimble into the driving hole in the center of the wheel; the wheel runs normally on the line; pull it out manually when there are 30 meters left at the bottom, Carry out manual welding in advance.
[0046] Step 2: Soldering
[0047] Turn on the power and turn on the switch of the butt welding machine; use the pedal to fix the two ends of the steel wire on the crimping clamps respectively, so that the two ends of the steel wire are aligned at the same length; adjust the current knob of the butt welding machine, press the butt welding switch, and then adjust the current to the steel wire Temper; grind the wire with an abrasive wheel grinder to make it smooth.
[0048] Step 3: Wash in hot wa...
Embodiment 2
[0073] A method for manufacturing a bead wire, comprising the following steps:
[0074] Step 1. Laying out
[0075] Check the steel number and specification of the incoming material; push the pre-prepared semi-finished wheel into the pay-off machine, press the "jacking" button to push the thimble into the driving hole in the center of the wheel; the wheel runs normally on the line; pull it out manually when there are 30 meters left at the bottom, Carry out manual welding in advance.
[0076] Step 2: Soldering
[0077] Turn on the power and turn on the switch of the butt welding machine; use the pedal to fix the two ends of the steel wire on the crimping clamps respectively, so that the two ends of the steel wire are aligned at the same length; adjust the current knob of the butt welding machine, press the butt welding switch, and then adjust the current to the steel wire Temper; grind the wire with an abrasive wheel grinder to make it smooth.
[0078] Step 3: Wash in hot wa...
Embodiment 3
[0103] A method for manufacturing a bead wire, comprising the following steps:
[0104] Step 1. Laying out
[0105] Check the steel number and specification of the incoming material; push the pre-prepared semi-finished wheel into the pay-off machine, press the "jacking" button to push the thimble into the driving hole in the center of the wheel; the wheel runs normally on the line; pull it out manually when there are 30 meters left at the bottom, Carry out manual welding in advance.
[0106] Step 2: Soldering
[0107] Turn on the power and turn on the switch of the butt welding machine; use the pedal to fix the two ends of the steel wire on the crimping clamps respectively, so that the two ends of the steel wire are aligned at the same length; adjust the current knob of the butt welding machine, press the butt welding switch, and then adjust the current to the steel wire Temper; grind the wire with an abrasive wheel grinder to make it smooth.
[0108] Step 3: Wash in hot wa...
PUM
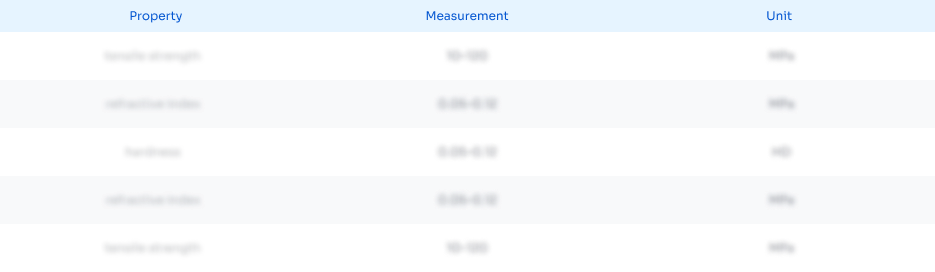
Abstract
Description
Claims
Application Information

- R&D Engineer
- R&D Manager
- IP Professional
- Industry Leading Data Capabilities
- Powerful AI technology
- Patent DNA Extraction
Browse by: Latest US Patents, China's latest patents, Technical Efficacy Thesaurus, Application Domain, Technology Topic, Popular Technical Reports.
© 2024 PatSnap. All rights reserved.Legal|Privacy policy|Modern Slavery Act Transparency Statement|Sitemap|About US| Contact US: help@patsnap.com