Production process of neopentyl glycol
A neopentyl glycol, production process technology, applied in the preparation of organic compounds, separation/purification of hydroxyl compounds, carbon-based compound preparation, etc., can solve the problems of high product prices, large differences, dark gray or gray color, etc. Achieve the effects of accelerated hydrogenation reaction rate, low equipment requirements, and low production costs
- Summary
- Abstract
- Description
- Claims
- Application Information
AI Technical Summary
Problems solved by technology
Method used
Examples
Embodiment 1
[0030] The preparation method of neopentyl glycol:
[0031] (1) Mix formaldehyde, isobutyraldehyde and triethylamine at a molar ratio of 1.3:1.2:0.2, and condense for 3 hours at a temperature of 80°C and a pressure of 1.5MPa to obtain a hydroxyvaleraldehyde solution;
[0032] (2) add methyl alcohol and catalyzer in the hydroxyvaleraldehyde solution gained in (1), the addition of formaldehyde is 15% of the hydroxyvaleraldehyde solution weight, the addition of catalyzer is 3% of the hydroxyvaleraldehyde solution weight, at temperature Hydrogenation reaction at 150°C and pressure of 10MPa for 2h to obtain neopentyl glycol solution;
[0033] (3) The neopentyl glycol solution obtained in (2) is purified to obtain the neopentyl glycol finished product.
[0034] Purification method of neopentyl glycol solution:
[0035] (1) The neopentyl glycol solution of gained is extracted with the petroleum ether of 15% of neopentyl glycol solution weight, obtains neopentyl glycol crude product...
Embodiment 2
[0039] The preparation method of neopentyl glycol:
[0040] (1) Mix formaldehyde, isobutyraldehyde and triethylamine at a molar ratio of 1:1:0.1, and condense for 2 hours at a temperature of 75°C and a pressure of 1 MPa to obtain a hydroxyvaleraldehyde solution;
[0041] (2) add methyl alcohol and catalyzer in the hydroxyvaleraldehyde solution gained in (1), the addition of formaldehyde is 15% of the hydroxyvaleraldehyde solution weight, the addition of catalyzer is 3% of the hydroxyvaleraldehyde solution weight, at temperature Hydrogenation at 130°C and pressure of 8 MPa for 1 hour to obtain neopentyl glycol solution;
[0042] (3) The neopentyl glycol solution obtained in (2) is purified to obtain the neopentyl glycol finished product.
[0043] Purification method of neopentyl glycol solution:
[0044] (1) The neopentyl glycol solution of gained is extracted with the petroleum ether of 15% of neopentyl glycol solution weight, obtains neopentyl glycol crude product;
[0045...
Embodiment 3
[0048] The preparation method of neopentyl glycol:
[0049] (1) Mix formaldehyde, isobutyraldehyde and triethylamine at a molar ratio of 1:1:0.2, and condense for 2 hours at a temperature of 65°C and a pressure of 0.5MPa to obtain a hydroxyvaleraldehyde solution;
[0050] (2) add methyl alcohol and catalyzer in the hydroxyvaleraldehyde solution gained in (1), the addition of formaldehyde is 15% of the hydroxyvaleraldehyde solution weight, the addition of catalyzer is 3% of the hydroxyvaleraldehyde solution weight, at temperature Hydrogenation at 100°C and pressure of 2 MPa for 1 hour to obtain neopentyl glycol solution;
[0051] (3) The neopentyl glycol solution obtained in (2) is purified to obtain the neopentyl glycol finished product.
[0052] Purification method of neopentyl glycol solution:
[0053] (1) The neopentyl glycol solution of gained is extracted with the petroleum ether of 15% of neopentyl glycol solution weight, obtains neopentyl glycol crude product;
[005...
PUM
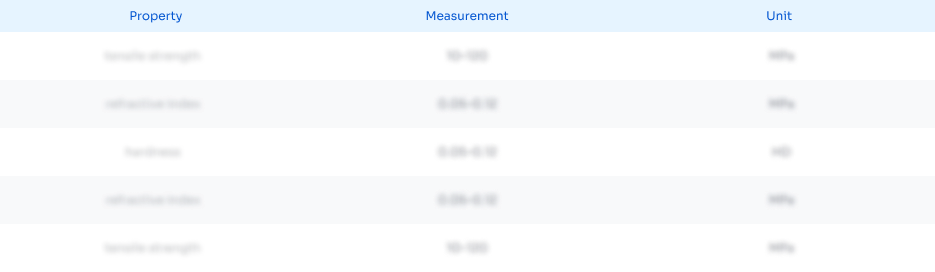
Abstract
Description
Claims
Application Information

- R&D
- Intellectual Property
- Life Sciences
- Materials
- Tech Scout
- Unparalleled Data Quality
- Higher Quality Content
- 60% Fewer Hallucinations
Browse by: Latest US Patents, China's latest patents, Technical Efficacy Thesaurus, Application Domain, Technology Topic, Popular Technical Reports.
© 2025 PatSnap. All rights reserved.Legal|Privacy policy|Modern Slavery Act Transparency Statement|Sitemap|About US| Contact US: help@patsnap.com