A kind of flotation separation method for separating copper oxide ore and talc
A technology of copper oxide and talc, applied in flotation, solid separation, etc., can solve the problems of copper concentrate recovery rate impact, lower copper recovery rate, large consumption of chemicals, etc., achieve good selectivity and collection performance, and inhibit talc Minerals, little effect on environmental pollution
- Summary
- Abstract
- Description
- Claims
- Application Information
AI Technical Summary
Problems solved by technology
Method used
Image
Examples
Embodiment 1
[0026] A copper oxide ore, the raw ore copper grade is about 3.85%, the copper in the raw ore is mainly malachite and azurite, and the gangue minerals are mainly talc and quartz.
[0027] The raw ore is milled by adding sodium sulfide to the fineness of 68%-74μm, the pH value of the pulp is 10.4, adding 180g / t cyclic sodium pyrophosphate as the pulp dispersant, adding 250g / ton magnesium sulfate and 40g / ton polyacrylamide valerate After fully stirring, 120g / ton of diethylaminobutyl xanthate was added to obtain copper oxide coarse concentrate and rougher tailings by flotation. And the amount of diethylaminobutyl xanthate in sweep selection two is 30g / ton and 10g / ton respectively.
[0028] The roughing concentrate is added with magnesium sulfate and valerate polyacrylamide for selection. The dosage of magnesium sulfate and valerate polyacrylamide in selection 1, selection 2 and selection 3 is 50g / ton and 20g / ton respectively, 30g / ton and 10g / ton, 20g / ton and 10g / ton to obtain co...
Embodiment 2
[0036] A copper oxide mineral, the copper grade is about 2.05%, the copper minerals are mainly malachite, and the gangue minerals are mainly talc, kaolin, quartz and calcite.
[0037] The raw ore is milled with sodium sulfide, the fineness is 75%-74μm, the pH value of the pulp is 10.4, 200g / ton of cyclic sodium pyrophosphate and 300g / ton of water glass are added as pulp dispersants, and 300g / ton of magnesium sulfate and hydroxypentine are added. Acrylic acid polyacrylamide 50g / ton, after fully stirring, add diethylaminobutyl xanthate 100g / ton, flotation to obtain copper oxide coarse concentrate and rougher tailings, rougher tailings add diethylaminobutyl xanthate Carry out sweep selection, the amount of diethylaminobutyl xanthate in sweep selection one and sweep selection two is 30g / ton and 10g / ton respectively.
[0038] The roughing concentrate is added with magnesium sulfate and valerate polyacrylamide for selection. The dosage of magnesium sulfate and valerate polyacrylamid...
PUM
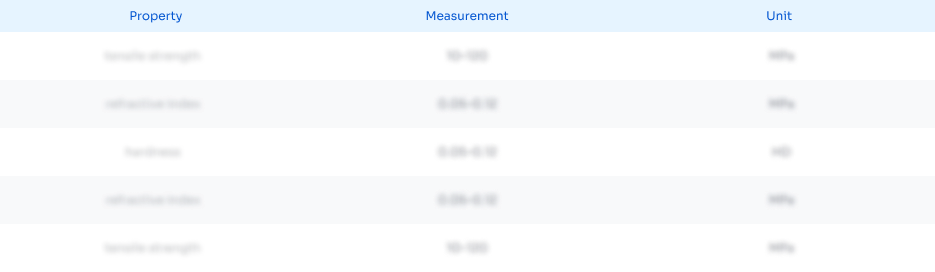
Abstract
Description
Claims
Application Information

- R&D Engineer
- R&D Manager
- IP Professional
- Industry Leading Data Capabilities
- Powerful AI technology
- Patent DNA Extraction
Browse by: Latest US Patents, China's latest patents, Technical Efficacy Thesaurus, Application Domain, Technology Topic, Popular Technical Reports.
© 2024 PatSnap. All rights reserved.Legal|Privacy policy|Modern Slavery Act Transparency Statement|Sitemap|About US| Contact US: help@patsnap.com