Dry etching equipment and etching method
A dry etching and equipment technology, used in electrical components, semiconductor/solid-state device manufacturing, circuits, etc., can solve problems such as extremely high requirements for cleanliness, increased manufacturing costs, and short maintenance cycles, and reduces requirements for cleanliness , The effect of maximizing production efficiency and prolonging maintenance cycle
- Summary
- Abstract
- Description
- Claims
- Application Information
AI Technical Summary
Problems solved by technology
Method used
Image
Examples
Embodiment 1
[0047] Please refer to figure 1 , Embodiment 1 of the dry etching equipment of the present invention, which includes: a main etching process chamber 210, a post-processing process chamber 310, and a transfer chamber 110, the main etching process chamber 210 and the post-processing process 310 chambers are respectively The transfer chamber 110 is connected and communicated through an openable and closable chamber door 600 , and the transfer chamber 110 is further provided with an openable and closable chamber door 600 to communicate with the outside world.
[0048] Such as figure 1 The product operation flow shown by the arrow, when performing etching treatment, the product to be processed first enters the transfer chamber 110, and then is transported by the transfer chamber 110 to a separate main etching process chamber 210 for the main etching process, and the post-processing process is carried out in another post-processing chamber. The processing is carried out in the proc...
PUM
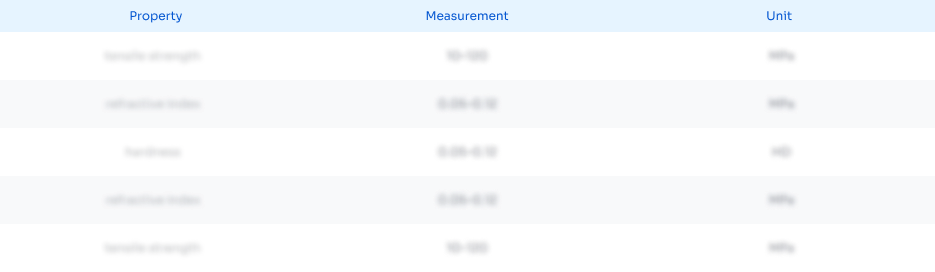
Abstract
Description
Claims
Application Information

- R&D
- Intellectual Property
- Life Sciences
- Materials
- Tech Scout
- Unparalleled Data Quality
- Higher Quality Content
- 60% Fewer Hallucinations
Browse by: Latest US Patents, China's latest patents, Technical Efficacy Thesaurus, Application Domain, Technology Topic, Popular Technical Reports.
© 2025 PatSnap. All rights reserved.Legal|Privacy policy|Modern Slavery Act Transparency Statement|Sitemap|About US| Contact US: help@patsnap.com