Preparation method for Al2O3 dispersion strengthened copper-based oil bearing
A technology of dispersion strengthened copper and dispersed copper, which is applied in the field of powder metallurgy, can solve problems such as low strength, poor wear resistance, and poor precision, and achieve excellent strength, excellent mechanical properties, and small dimensional changes
- Summary
- Abstract
- Description
- Claims
- Application Information
AI Technical Summary
Problems solved by technology
Method used
Examples
Embodiment 1
[0015] Example 1: 0.3wt%Al 2 o 3 Preparation of dispersion-strengthened copper-based oil-impregnated bearings
[0016] -150 micron dispersed copper alloy powder prepared by internal oxidation method (containing 0.3wt% Al 2 o 3 ) and commercially available -45 micron tin powder as raw materials, according to the mass ratio of dispersed copper alloy powder: tin powder = 91:9 to mix evenly, the mixed powder is subjected to 400 ℃, 6h diffusion alloying treatment in hydrogen, after crushing , sieve, and then mix the sieved powders with particle sizes of +150 microns, -150 microns to +75 microns, -75 microns to +45 microns and -45 microns in proportions of 3%, balance, 30% and 30%, A dispersed copper-tin diffusion alloyed powder is obtained. Use 100MPa forming pressure to mold the powder to prepare the bearing green body with a density of 6.1g / cm 3 . The obtained bearing green body was sintered in hydrogen at 800°C for 1 hour. The sintered billet is finished and vacuum-immers...
Embodiment 2
[0017] Example 2: 1wt%Al 2 o 3 Preparation of dispersion-strengthened copper-based oil-impregnated bearings
[0018] -150 micron dispersed copper alloy powder prepared by internal oxidation method (containing 1wt% Al 2 o 3 ) and commercially available -45 micron tin powder as raw materials, according to the mass ratio of dispersed copper alloy powder: tin powder = 90:10 to mix evenly, the mixed powder was subjected to 600 ℃, 4h diffusion alloying treatment in hydrogen, after crushing , sieve, and then mix the sieved powders with particle sizes of +150 microns, -150 microns to +75 microns, -75 microns to +45 microns and -45 microns in proportions of 5%, balance, 20% and 20%, A dispersed copper-tin diffusion alloyed powder is obtained. Using 200MPa forming pressure molding powder to prepare bearing green body, the density is 6.4g / cm 3 . The obtained bearing green body was sintered in hydrogen at 850°C for 2 hours. The sintered billet is finished and vacuum-immersed in oil...
Embodiment 3
[0019] Example 3: 2wt%Al 2 o 3 Preparation of dispersion-strengthened copper-based oil-impregnated bearings
[0020] -150 micron dispersed copper alloy powder prepared by internal oxidation method (containing 2wt% Al 2 o 3 ) and commercially available -45 micron tin powder as raw materials, according to the mass ratio of dispersed copper alloy powder: tin powder = 89:11 to mix evenly, the mixed powder is subjected to 700 ℃, 3h diffusion alloying treatment in hydrogen, after crushing , sieve, and then mix the sieved powders with particle sizes of +150 microns, -150 microns to +75 microns, -75 microns to +45 microns and -45 microns in proportions of 3%, balance, 30% and 30%, A dispersed copper-tin diffusion alloyed powder is obtained. Use 300MPa forming pressure to mold the powder to prepare the bearing green body with a density of 6.3g / cm 3 . The obtained bearing green body was sintered in hydrogen at 900°C for 3 hours. The sintered billet is finished and vacuum-immersed...
PUM
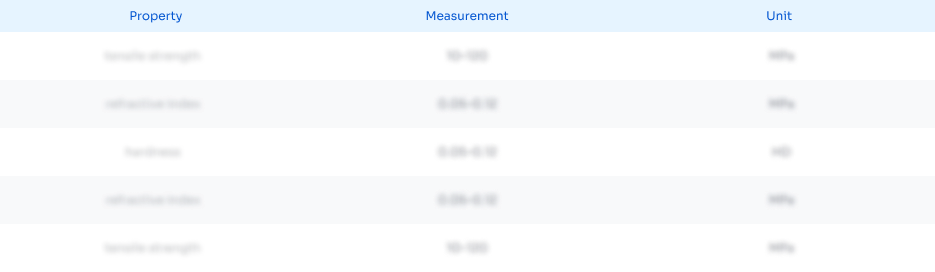
Abstract
Description
Claims
Application Information

- Generate Ideas
- Intellectual Property
- Life Sciences
- Materials
- Tech Scout
- Unparalleled Data Quality
- Higher Quality Content
- 60% Fewer Hallucinations
Browse by: Latest US Patents, China's latest patents, Technical Efficacy Thesaurus, Application Domain, Technology Topic, Popular Technical Reports.
© 2025 PatSnap. All rights reserved.Legal|Privacy policy|Modern Slavery Act Transparency Statement|Sitemap|About US| Contact US: help@patsnap.com