Ultralow boiler smoke emission device
A technology of emission device and boiler flue gas, applied in the field of flue gas purification, can solve the problem that denitrification, dust removal, and desulfurization technology cannot meet ultra-low emission standards, the flue gas particulate matter at the desulfurization outlet is increased, and desulfurization efficiency cannot meet ultra-low standards, etc. problems, to achieve the effect of reducing equipment operating costs, reducing pressure, and reducing NOX generation
- Summary
- Abstract
- Description
- Claims
- Application Information
AI Technical Summary
Problems solved by technology
Method used
Image
Examples
Embodiment Construction
[0023] like figure 1 As shown, a boiler flue gas ultra-low emission device according to the present invention includes a coal-fired boiler 1, a denitration reactor 2, a bag filter 3 and a desulfurization tower 4, and the flue gas generated by the coal-fired boiler 1 passes through the denitration reaction in sequence 2, bag filter 3 and desulfurization tower 4 and then discharged.
[0024] like figure 2 As shown, the coal-fired boiler 1 of the present invention includes a furnace 5, a main burner 6 and a flue 7, the main burner 6 is arranged at the bottom of the furnace 5, and the main burner 6 is sequentially provided with upper two Secondary air spout 8, last wind spout 9, middle secondary air spout 10, next air spout 11 and following secondary air spout 12, wherein the area of the last secondary air spout 8 and the middle secondary air spout 10 are 1 / 2 of the area of the lower secondary air spout 12. The dense phase side of the previous wind is at the bottom, the di...
PUM
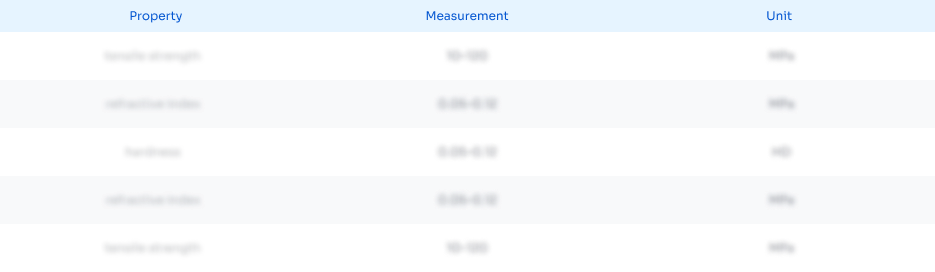
Abstract
Description
Claims
Application Information

- R&D
- Intellectual Property
- Life Sciences
- Materials
- Tech Scout
- Unparalleled Data Quality
- Higher Quality Content
- 60% Fewer Hallucinations
Browse by: Latest US Patents, China's latest patents, Technical Efficacy Thesaurus, Application Domain, Technology Topic, Popular Technical Reports.
© 2025 PatSnap. All rights reserved.Legal|Privacy policy|Modern Slavery Act Transparency Statement|Sitemap|About US| Contact US: help@patsnap.com