Sole material emulsifier and preparation method thereof
A shoe sole material and emulsifier technology, which is applied in the field of shoe sole materials, can solve problems such as insufficient toughness and tensile properties, and affect the service life of shoes, and achieve good emulsification effect, good emulsification effect, and simple preparation method.
- Summary
- Abstract
- Description
- Claims
- Application Information
AI Technical Summary
Problems solved by technology
Method used
Examples
Embodiment 1
[0017] An emulsifier for sole material, comprising the following raw materials in parts by weight: 5 parts of Artemisia annua extract, 2 parts of ionic emulsifier, 3 parts of nonionic emulsifier, 5 parts of polyamide, 3 parts of polyethylpolyamine, formazan 2 parts of methyl tert-butyl ether, 3 parts of ethyl tert-butyl ether, 0.5 parts of stabilizer, and 3.5 parts of defoamer.
[0018] The ionic emulsifier is selected from one of sodium lauryl silicate, lecithin, alkyl naphthalene sulfonate, sodium diisopropylnaphthalene sulfonate or a mixture thereof.
[0019] The nonionic emulsifier is selected from one or a mixture of lauryl alcohol polyoxyethylene ether, benzylphenol polyoxyethylene ether, fatty acid methyl ester polyoxyethylene ether and styrene ethylphenol polyoxyethylene ether.
[0020] The polyethyl polyamine is a mixture of diethylenetriamine and tetraethylenepentamine, and its molar ratio is 1.5.
[0021] A preparation method for sole material emulsifier mainly com...
Embodiment 2
[0027] An emulsifier for sole material, comprising the following raw materials in parts by weight: 7 parts of Artemisia annua extract, 5 parts of ionic emulsifier, 7 parts of nonionic emulsifier, 6 parts of polyamide, 5 parts of polyethyl polyamine, formazan 6 parts of methyl tert-butyl ether, 5 parts of ethyl tert-butyl ether, 2.5 parts of stabilizer, and 4.5 parts of defoamer.
[0028] The ionic emulsifier is selected from one of sodium lauryl silicate, lecithin, alkyl naphthalene sulfonate, sodium diisopropylnaphthalene sulfonate or a mixture thereof.
[0029] The nonionic emulsifier is selected from one or a mixture of lauryl alcohol polyoxyethylene ether, benzylphenol polyoxyethylene ether, fatty acid methyl ester polyoxyethylene ether and styrene ethylphenol polyoxyethylene ether.
[0030] The polyethyl polyamine is a mixture of diethylenetriamine and tetraethylenepentamine, and its molar ratio is 2.0.
[0031] A preparation method for sole material emulsifier mainly co...
Embodiment 3
[0037] An emulsifier for sole material, comprising the following raw materials in parts by weight: 10 parts of Artemisia annua extract, 9 parts of ionic emulsifier, 10 parts of nonionic emulsifier, 7 parts of polyamide, 7 parts of polyethylpolyamine, formazan 10 parts of methyl tert-butyl ether, 8 parts of ethyl tert-butyl ether, 3.5 parts of stabilizer, and 6.5 parts of defoamer.
[0038] The ionic emulsifier is selected from one of sodium lauryl silicate, lecithin, alkyl naphthalene sulfonate, sodium diisopropylnaphthalene sulfonate or a mixture thereof.
[0039] The nonionic emulsifier is selected from one or a mixture of lauryl alcohol polyoxyethylene ether, benzylphenol polyoxyethylene ether, fatty acid methyl ester polyoxyethylene ether and styrene ethylphenol polyoxyethylene ether.
[0040] The polyethylpolyamine is a mixture of diethylenetriamine and tetraethylenepentamine, and its molar ratio is 2.5.
[0041] A preparation method for sole material emulsifier mainly c...
PUM
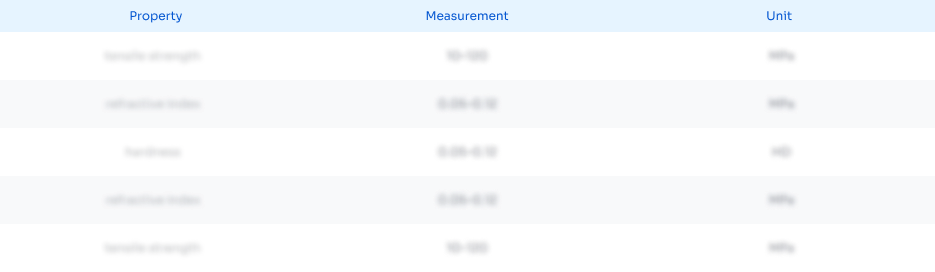
Abstract
Description
Claims
Application Information

- R&D Engineer
- R&D Manager
- IP Professional
- Industry Leading Data Capabilities
- Powerful AI technology
- Patent DNA Extraction
Browse by: Latest US Patents, China's latest patents, Technical Efficacy Thesaurus, Application Domain, Technology Topic, Popular Technical Reports.
© 2024 PatSnap. All rights reserved.Legal|Privacy policy|Modern Slavery Act Transparency Statement|Sitemap|About US| Contact US: help@patsnap.com