Multi-step efficient enzyme hydrolysis process method of lignocellulose
A technology of lignocellulose and process method, which is applied in the direction of fermentation, etc., can solve the problems of increasing production cost, post-treatment process complexity, complex reactor design, large amount of cellulase, etc., to reduce concentration cost, reduce water consumption, The effect of low investment cost
- Summary
- Abstract
- Description
- Claims
- Application Information
AI Technical Summary
Problems solved by technology
Method used
Image
Examples
Embodiment 1
[0030] The lignocellulose of wheat straw after 20wt% ammonium sulfite delignification treatment (140°C, 2 hours, liquid-to-solid ratio 6) was used as the substrate of enzymatic hydrolysis for two-stage enzymatic hydrolysis to sugar production. The specific reaction conditions of 1# and 2# enzymatic hydrolysis tanks are respectively: enzyme consumption is 11FPU / g substrate and 4FPU / g substrate (enzyme total consumption 15FPU / g substrate); Enzyme hydrolysis time is 36 hours and 12 hours ( The total reaction time is 48 hours); the temperature, substrate concentration and pH value of each stage of enzymatic hydrolysis are 50° C., 8% and 4.8. When the sixth batch of enzymatic hydrolysis of lignocellulosic raw materials was carried out, the enzymatic hydrolysis system reached a stable production state. At this time, the sugar concentration obtained by the 1# enzyme hydrolysis tank is about 53g / L, and the total sugar conversion rate of the substrate is 82%.
[0031] The shape change...
Embodiment 2
[0033]Using commercial bleached softwood pulp as raw material (enzymatic hydrolysis substrate), directly adopt 3-stage enzymatic hydrolysis to produce sugar. The specific reaction conditions of 1#, 2# and 3# enzyme hydrolysis tanks are: enzyme dosage 20FPU / g substrate, 5FPU / g substrate and 5FPU / g substrate (total enzyme dosage 30FPU / g substrate); enzyme hydrolysis The time is 48 hours, 12 hours and 12 hours (the total reaction time is 72 hours); the substrate concentration is 20%, 15% and 10%; the temperature and pH value of each stage of enzymatic hydrolysis are 50°C and 4.8. When the enzymatic hydrolysis of the eighth batch of lignocellulosic raw materials was carried out, the enzymatic hydrolysis system reached a stable production state. At this time, the sugar concentration obtained by the 1# enzyme hydrolysis tank is about 126g / L, and the total sugar conversion rate of the substrate is 77%.
Embodiment 3
[0035] After corn stalks were delignified with 12wt% NaOH (130° C., 2 hours, liquid-solid ratio 6), three stages of enzymatic hydrolysis for sugar production were carried out. The specific reaction conditions of 1#, 2# and 3# enzyme hydrolysis tanks are respectively: the enzyme dosage is 12FPU / g substrate, 5FPU / g substrate and 3FPU / g substrate (the total enzyme dosage is 20FPU / g substrate); The hydrolysis time is 24 hours, 12 hours and 12 hours (the total reaction time is 48 hours); the temperature, substrate concentration and pH value of each stage of enzyme hydrolysis are 50° C., 12% and 4.8. When the enzymatic hydrolysis of the eighth batch of lignocellulosic raw materials was carried out, the enzymatic hydrolysis system reached a stable production state. At this time, the sugar concentration of the product obtained by the 1# enzyme hydrolysis tank is about 82g / L, and the conversion rate of the total sugar of the substrate is 83%.
PUM
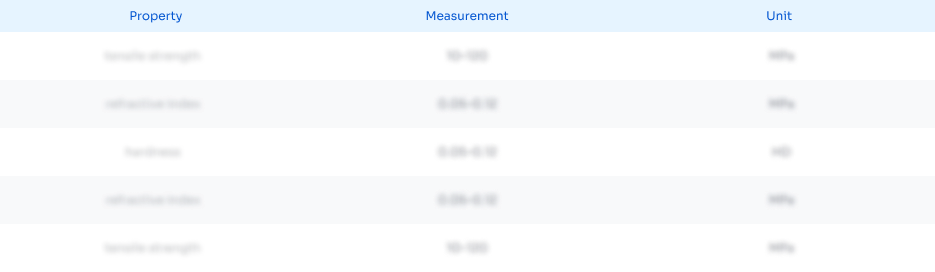
Abstract
Description
Claims
Application Information

- R&D Engineer
- R&D Manager
- IP Professional
- Industry Leading Data Capabilities
- Powerful AI technology
- Patent DNA Extraction
Browse by: Latest US Patents, China's latest patents, Technical Efficacy Thesaurus, Application Domain, Technology Topic, Popular Technical Reports.
© 2024 PatSnap. All rights reserved.Legal|Privacy policy|Modern Slavery Act Transparency Statement|Sitemap|About US| Contact US: help@patsnap.com