Method for preparing tetramethyl orthosilicate in direct method
A tetramethoxysilane, direct method technology, applied in the direction of silicon organic compounds, etc., can solve the problems of atmospheric environmental pollution, complex rectification and purification, complicated operation, etc., and achieves the effect of large contact surface, favorable reaction and low price.
- Summary
- Abstract
- Description
- Claims
- Application Information
AI Technical Summary
Problems solved by technology
Method used
Image
Examples
Embodiment 1
[0031] Weigh 40g of silicon powder and 3.2g of Cu on an electronic balance 2 O, mix, stir evenly, pour into pulverizer and pulverize, pulverize time 1min. Take 30mL of pulverized silicon powder and cuprous oxide and pour it into a fixed bed reactor, combine the fixed bed reactor, and place it in a circulating tube furnace. Nitrogen was introduced into the fixed bed reactor with a nitrogen flow rate of 15mL / min. The temperature program was started, with an initial temperature of 15°C and a final temperature of 240°C. The heating time was 1h, and the temperature was maintained at 240°C for 4h. Then, switch to methanol, methanol flow rate 0.1mL / min, first react for 0.5h, then start timing, react at 220°C for 1h, take samples with a centrifuge tube, and perform detection on a gas chromatograph. Calculate the conversion of methanol and the selectivity of tetramethoxysilane. Experimental results such as figure 1 .
Embodiment 2
[0033] Weigh 40g of silicon powder and 3.2g of Cu on an electronic balance 2 O, mix, stir evenly, pour into pulverizer and pulverize, pulverize time 1min. Take 30mL of pulverized silicon powder and cuprous oxide and pour it into a fixed bed reactor, combine the fixed bed reactor, and place it in a circulating tube furnace. Nitrogen was introduced into the fixed bed reactor with a nitrogen flow rate of 15mL / min. The temperature program was started, with an initial temperature of 15°C and a final temperature of 240°C. The heating time was 1h, and the temperature was maintained at 240°C for 4h. Then, switch to methanol, methanol flow rate 0.1mL / min, react for 0.5h first, then start timing, react at 240°C for 1h each, take samples with a centrifuge tube, and perform detection on a gas chromatograph. Calculate the conversion of methanol and the selectivity of tetramethoxysilane. Experimental results such as figure 1 .
Embodiment 3
[0035] Weigh 40g of silicon powder and 3.2g of Cu on an electronic balance 2 O, mix, stir evenly, pour into pulverizer and pulverize, pulverize time 1min. Take 30mL of pulverized silicon powder and cuprous oxide and pour it into a fixed bed reactor, combine the fixed bed reactor, and place it in a circulating tube furnace. Nitrogen was introduced into the fixed bed reactor with a nitrogen flow rate of 15mL / min. The temperature program was started, with an initial temperature of 15°C and a final temperature of 240°C. The heating time was 1h, and the temperature was maintained at 240°C for 4h. Then, switch to methanol, methanol flow rate 0.1mL / min, first react for 0.5h, then start timing, react at 260°C for 1h each, take samples with a centrifuge tube, and perform detection on a gas chromatograph. Calculate the conversion of methanol and the selectivity of tetramethoxysilane. Experimental results such as figure 1 .
PUM
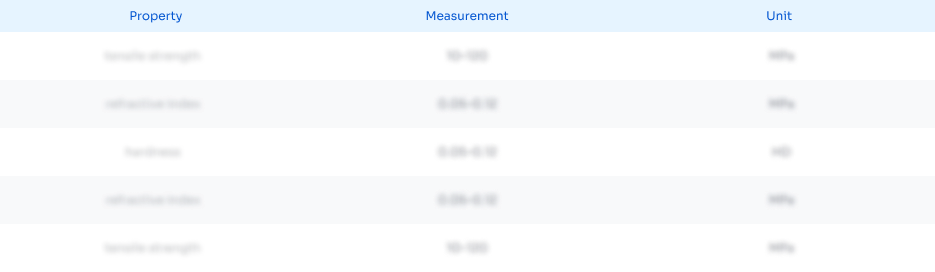
Abstract
Description
Claims
Application Information

- R&D Engineer
- R&D Manager
- IP Professional
- Industry Leading Data Capabilities
- Powerful AI technology
- Patent DNA Extraction
Browse by: Latest US Patents, China's latest patents, Technical Efficacy Thesaurus, Application Domain, Technology Topic, Popular Technical Reports.
© 2024 PatSnap. All rights reserved.Legal|Privacy policy|Modern Slavery Act Transparency Statement|Sitemap|About US| Contact US: help@patsnap.com