Vanadium-free denitration catalyst for reducing SO2 oxidization rate and preparation method thereof
A technology of denitrification catalyst and oxidation rate, which is applied in the direction of catalyst activation/preparation, physical/chemical process catalysts, chemical instruments and methods, etc. It can solve the problems of unstable activity and unbalanced active centers, and achieve uniform dispersion and good catalyst activity. , the effect of tight connection
- Summary
- Abstract
- Description
- Claims
- Application Information
AI Technical Summary
Problems solved by technology
Method used
Image
Examples
Embodiment 1
[0038] will contain TiO 2 500g of titanyl sulfate is dissolved in the sulfuric acid solution, adding 3 A total of 22.5g of ammonium metatungstate solution, with CeO 2 40g of cerium nitrate solution to form TiO 2 It is a 35g / L mixed solution. After stirring for 2 hours, gradually add ammonia water to adjust the pH value to 9.5. After the precipitation is complete, filter, wash, and dry, and roast at 620°C for 8 hours; after roasting, the powder is mixed with WO 3 A total of 7.5g of ammonium metatungstate solution was made into a slurry with a water content of 30%. After stirring, 4g of polyethylene oxide was added, stirred for 40min, sealed and left for 24h, and dried; The denitration catalyst was obtained after soaking in 10% ethanol solution of ethyl ester for 15 seconds, filtering, drying, and roasting at 620° C. for 8 hours. The fresh catalyst obtained above and the catalyst after high-temperature mixing with catalytic cracking vanadium-containing spent catalyst (LDC ser...
Embodiment 2
[0042] will contain TiO 2 500g of titanyl sulfate is dissolved in the sulfuric acid solution, and the 3 A total of 20g of ammonium metatungstate solution to form TiO 2 35g / L mixed solution, with CeO 2 Calculate 30g of cerium nitrate solution, stir for 2 hours, gradually add ammonia water to adjust the pH value to 8.5, after the precipitation is complete, filter, wash, dry, and roast at 600°C for 8 hours; after roasting, the powder is mixed with MoO 3 A total of 6g of ammonium metatungstate solution was used to make a slurry with a water content of 30%. After stirring, 4g of polyethylene oxide was added, stirred for 40min, sealed and left for 24h, and dried; The denitrification catalyst was obtained by immersing in 5% ethanol solution of the ester for 10 seconds, filtering, drying, and roasting at 600° C. for 8 hours. The fresh catalyst obtained above and the catalyst after high-temperature mixing with catalytic cracking vanadium-containing spent catalyst (LDC series) were e...
Embodiment 3
[0046] will contain TiO 2 500g of titanyl sulfate is dissolved in the sulfuric acid solution, and the 3 20g of ammonium metatungstate, expressed as WO 3 20g of ammonium metatungstate solution, with CeO 2 25g of cerium nitrate solution to form TiO 2 It is a 35g / L mixed solution. After stirring for 2 hours, gradually add ammonia water to adjust the pH value to 8.5. After the precipitation is complete, filter, wash, and dry, and roast at 600°C for 8 hours; after roasting, the powder is mixed with MoO 3 A total of 6g of ammonium metatungstate solution was made into a slurry with a water content of 30%. After stirring, 3.5g of polyethylene oxide was added, stirred for 40min, sealed and left for 24h, and dried; The denitration catalyst was obtained after 6 seconds in 8% ethyl ester ethanol solution, filtered, dried, and calcined at 600° C. for 8 hours. The fresh catalyst obtained above and the catalyst after high-temperature mixing with catalytic cracking vanadium-containing spe...
PUM
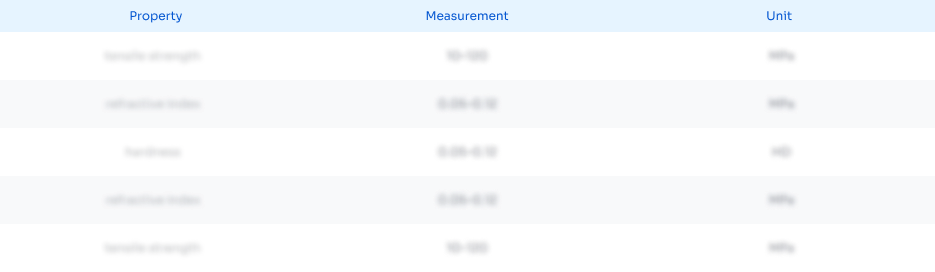
Abstract
Description
Claims
Application Information

- R&D Engineer
- R&D Manager
- IP Professional
- Industry Leading Data Capabilities
- Powerful AI technology
- Patent DNA Extraction
Browse by: Latest US Patents, China's latest patents, Technical Efficacy Thesaurus, Application Domain, Technology Topic, Popular Technical Reports.
© 2024 PatSnap. All rights reserved.Legal|Privacy policy|Modern Slavery Act Transparency Statement|Sitemap|About US| Contact US: help@patsnap.com