Heat treatment technology for engine shield
An engine shield and process technology, applied in the field of mechanical processing, can solve the problems of difficulty in obtaining comprehensive performance indicators, insufficient cooling, insufficient cooling, etc., and achieve the effects of easy promotion and use, long water cooling time, and fast water entry speed.
- Summary
- Abstract
- Description
- Claims
- Application Information
AI Technical Summary
Problems solved by technology
Method used
Examples
Embodiment 1
[0026] The engine guard quenched and tempered steel used for the heat treatment process includes the following components by weight percentage: C 0.52%, Cr 1.07%, Si 0.46%, Mn 0.81%, Ni 0.03%, Ti 0.94%, the balance is Fe and non-removable The trace elements, and the non-removable trace elements ≤0.05%.
[0027] A heat treatment process for engine guards, according to the following steps:
[0028] (1) Normalizing: the engine shield after casting is subjected to the second normalizing treatment, the specific operation is: before the first normalizing, the temperature of the shield is 680℃, the temperature is kept for 3h, and then the temperature is raised for the first normalization. Fire; the temperature of the first normalizing is increased to 860℃ and the temperature is kept for 2h; after that, it is air-cooled to 380℃; before the second normalizing, the temperature of the shield is put into the furnace at 340℃, the temperature is kept for 4h, and then the temperature is increased...
Embodiment 2
[0033] The quenched and tempered steel for the engine cover for the heat treatment process includes the following components by weight percentage: C 0.60%, Cr 1.21%, Si 0.66%, Mn 0.92%, Ni 0.04%, Ti 1.08%, the balance is Fe and non-removable The trace elements, and the non-removable trace elements ≤0.05%.
[0034] A heat treatment process for engine guards, according to the following steps:
[0035] (1) Normalizing; the engine shield after casting is subjected to secondary normalizing treatment, the specific operation is: before the first normalizing, the temperature of the shield is 690℃, the temperature is maintained for 3.5h, and then the temperature is raised for the first time Normalizing; the temperature of the first normalizing is raised to 880℃ and holding for 2.5h; after that, it is air-cooled to 390℃; before the second normalizing, the temperature of the shield is put into the furnace at 350℃, holding for 4.5h, then heating to 700℃, Keep the temperature for 3.2h; then in...
Embodiment 3
[0040] The engine guard quenched and tempered steel used for the heat treatment process includes the following components by weight percentage: C 0.86%, Cr 1.60%, Si 0.83%, Mn 1.10%, Ni 0.05%, Ti 1.23%, the balance is Fe and non-removable The trace elements, and the non-removable trace elements ≤0.05%.
[0041] A heat treatment process for engine guards, according to the following steps:
[0042] (1) Normalizing; the engine shield after casting is subjected to the second normalizing treatment, the specific operation is: before the first normalizing, the temperature of the shield is 700 ℃, the heat preservation is 4h, and then the temperature is raised for the first normalization. Fire; the first normalizing heats up to 900℃ and keeps it for 3h; then air-cools to 400℃; before the second normalizing, put the shield into the furnace at 360℃, keep it for 5h, then raise it to 720℃, keep it for 3.5h ; Then the temperature is increased for the second normalizing; the second normalizing i...
PUM
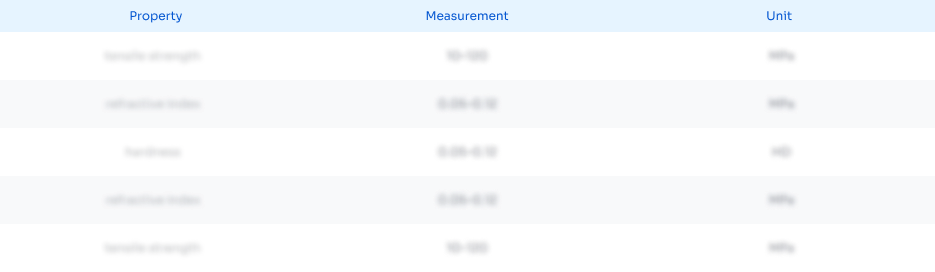
Abstract
Description
Claims
Application Information

- Generate Ideas
- Intellectual Property
- Life Sciences
- Materials
- Tech Scout
- Unparalleled Data Quality
- Higher Quality Content
- 60% Fewer Hallucinations
Browse by: Latest US Patents, China's latest patents, Technical Efficacy Thesaurus, Application Domain, Technology Topic, Popular Technical Reports.
© 2025 PatSnap. All rights reserved.Legal|Privacy policy|Modern Slavery Act Transparency Statement|Sitemap|About US| Contact US: help@patsnap.com