Torque ripple minimization fault-tolerance control method in loss of phase of six-phase motor
A torque ripple, fault-tolerant control technology, applied in torque ripple control, motor generator control, electronic commutation motor control, etc., can solve problems such as motor fluctuations, and achieve the effect of improving response speed and fault tolerance.
- Summary
- Abstract
- Description
- Claims
- Application Information
AI Technical Summary
Problems solved by technology
Method used
Image
Examples
Embodiment example
[0067] The six-phase winding can be arranged into a symmetrical six-phase winding with a phase angle of 60° and an asymmetrical six-phase winding with a phase angle of 30° from the perspective of the spatial arrangement of the winding. However, the harmonic content of the magnetomotive force of the symmetrical six-phase motor is twice that of the asymmetrical six-phase motor. Too much harmonics of the magnetomotive force will increase the loss of the permanent magnet of the motor and affect the torque fluctuation of the motor. Therefore, the present invention mainly Asymmetric six-phase windings are studied. The asymmetrical six-phase winding can also be called the six-phase double Y-shifted 30° winding, which is composed of two sets of three-phase windings with a mutual difference of 120° electrical angle, and the two sets of windings have a mutual difference of 30° electrical angle.
[0068] Such as figure 1 As shown, it is the spatial distribution diagram of the six-phase ...
PUM
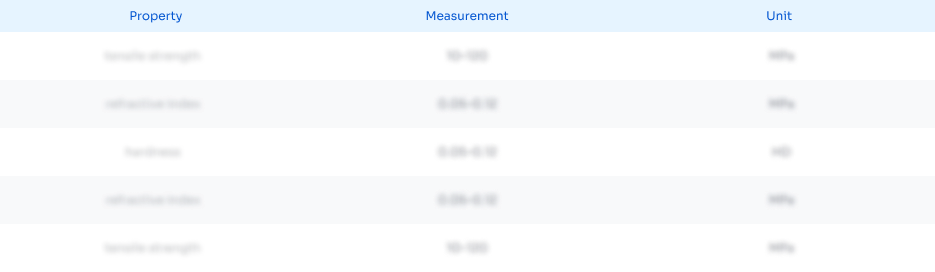
Abstract
Description
Claims
Application Information

- R&D Engineer
- R&D Manager
- IP Professional
- Industry Leading Data Capabilities
- Powerful AI technology
- Patent DNA Extraction
Browse by: Latest US Patents, China's latest patents, Technical Efficacy Thesaurus, Application Domain, Technology Topic, Popular Technical Reports.
© 2024 PatSnap. All rights reserved.Legal|Privacy policy|Modern Slavery Act Transparency Statement|Sitemap|About US| Contact US: help@patsnap.com