Method for producing copper sulphate and recycling ferro-nickel through vulcanization of albata waste by pyrite
A technology of copper-nickel sulfide and nickel-iron alloy, which is applied in the field of producing copper matte from pyrite copper-nickel sulfide alloy waste and recycling nickel-iron alloy, which can solve the problems of low copper ore mining capacity, low copper, and exhaustion of raw ore resources. Low maintenance cost, simple operation, and environmental protection in the process
- Summary
- Abstract
- Description
- Claims
- Application Information
AI Technical Summary
Problems solved by technology
Method used
Image
Examples
Embodiment 1
[0018] Such as figure 1 As shown, the method for making copper matte from copper-nickel alloy waste of pyrite sulfide and reclaiming nickel-iron alloy is as follows: first, 30 g of copper-nickel-iron alloy waste (Cu70wt%, Ni27.7wt%, Fe2.3wt%) are crushed to After the piece size is 20-30mm and the moisture content is lower than 3%, when the copper-nickel-iron alloy waste is completely melted at 1400°C, under the condition of feeding inert gas (the inert gas is nitrogen, the flow rate is 300ml / min, spray Blowing pressure is 0.2MP), add 23.5g pyrite with moisture content less than 3%, 0.2~0.4mm (the ratio of sulfur in pyrite to copper S / Cu in copper-nickel-iron alloy scrap is 1.2 : 1. Pyrite is sprayed through the spray gun, and the injection pressure is 0.5MPa) to carry out the vulcanization reaction at a temperature of 1450°C for 1h, and continue to feed inert gas at 1450-1500°C for a heat preservation reaction for 60min. After the reaction, the copper matte and After the nick...
Embodiment 2
[0021] Such as figure 1 As shown, the method for making copper matte from pyrite sulfide copper-nickel alloy waste and reclaiming nickel-iron alloy is as follows: first, copper-nickel-iron alloy waste (Cu70wt%, Ni27.7wt%, Fe2.3wt%) is crushed to a block size 100 ~ 150mm, dried to less than 3% moisture, when the copper-nickel-iron alloy waste is completely melted at 1500 ℃, under the condition of feeding inert gas (the inert gas is argon, the flow rate is 500ml / min, spray Pressure is 1.5MP), add 31.5g of pyrite with water content less than 3%, 0.2-0.4mm (the amount of S / Cu of sulfur in pyrite and copper in copper-nickel-iron alloy scrap is 1.6:1, Pyrite is sprayed through the spray gun, the injection pressure is 1.5MPa) and the vulcanization reaction is carried out at a temperature of 1600°C for 3 hours, and the inert gas is continued to be introduced at 1550-1600°C for a heat preservation reaction for 60 minutes. After the reaction, the copper matte and nickel-iron moisture A...
Embodiment 3
[0024] Such as figure 1 As shown, the method for making copper matte from pyrite sulfide copper-nickel alloy waste and reclaiming nickel-iron alloy is as follows: first, copper-nickel-iron alloy waste (Cu70wt%, Ni27.7wt%, Fe2.3wt%) is crushed to a block size 250 ~ 300mm, dried until the moisture content is less than 3%, when the copper-nickel-iron alloy waste is completely melted at 1400 ℃, under the condition of feeding inert gas (the inert gas is argon, the flow rate is 800ml / min, spray Pressure is 1.0MP), add 27.55g of pyrite with water content less than 3% and 0.2-0.4mm (the amount of S / Cu of sulfur in pyrite and copper in copper-nickel-iron alloy scrap is 1.4:1, Pyrite is sprayed through a spray gun, and the injection pressure is 1.0MPa) and the vulcanization reaction is carried out at a temperature of 1400 ° C for 2.5 hours, and the inert gas is continued to be introduced at 1400 ~ 1450 ° C for a heat preservation reaction for 60 minutes. After layering, let stand for 0...
PUM
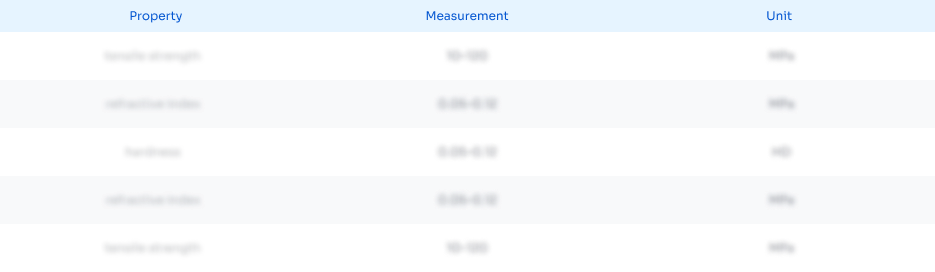
Abstract
Description
Claims
Application Information

- Generate Ideas
- Intellectual Property
- Life Sciences
- Materials
- Tech Scout
- Unparalleled Data Quality
- Higher Quality Content
- 60% Fewer Hallucinations
Browse by: Latest US Patents, China's latest patents, Technical Efficacy Thesaurus, Application Domain, Technology Topic, Popular Technical Reports.
© 2025 PatSnap. All rights reserved.Legal|Privacy policy|Modern Slavery Act Transparency Statement|Sitemap|About US| Contact US: help@patsnap.com