Device and method for driving plate hole flanging forming through multidirectional magnetic field force
A magnetic field force, plate technology, applied in forming tools, metal processing equipment, manufacturing tools, etc., can solve problems such as wrinkling of sheet flanges, and achieve the effects of avoiding cracks, increasing the height of turning holes, and reducing the value of tensile stress.
- Summary
- Abstract
- Description
- Claims
- Application Information
AI Technical Summary
Problems solved by technology
Method used
Image
Examples
Embodiment 1
[0048] Such as Figure 4 and Figure 5 As shown, a device of the present invention that utilizes multi-directional magnetic force to drive plate hole turning and forming, the device includes a blank holder 1 and a die 2, and the blank holder 1 is placed above the die 2. The blank holder 1 is used to press the plate 3 to be formed by turning holes between the blank holder 1 and the die 2 . The die 2 has a die cavity 4 inside. On the blank holder 1 and the die 2, an upper coil groove and a lower coil groove are respectively arranged oppositely, and an upper-end reducing coil 5 is embedded in the upper coil groove, and a lower end coil 5 is embedded in the lower coil groove. Part of the reduced diameter coil 6. A prefabricated hole is opened on the plate 3, an axial drawing coil 7 is arranged above the edge of the prefabricated hole of the plate 3, and an internal bulging coil 8 is arranged in the prefabricated hole of the plate 3. The internal bulging coil 8 comprises vertic...
Embodiment 2
[0053] Such as Figure 6 to Figure 9 As shown, a device of the present invention that utilizes multi-directional magnetic force to drive plate hole turning and forming, the device includes a blank holder 1 and a die 2, and the blank holder 1 is placed above the die 2. The blank holder 1 is used to press the plate 3 to be formed by turning holes between the blank holder 1 and the die 2 . The die 2 has a die cavity 4 inside. On the blank holder 1 and the die 2, an upper coil groove and a lower coil groove are respectively arranged oppositely, and an upper-end reducing coil 5 is embedded in the upper coil groove, and a lower end coil 5 is embedded in the lower coil groove. Part of the reduced diameter coil 6. A prefabricated hole is opened on the plate 3, an axial drawing coil 7 is arranged above the edge of the prefabricated hole of the plate 3, and an internal bulging coil 8 is arranged in the prefabricated hole of the plate 3. Die 2 is placed on a base plate 9, and base pla...
PUM
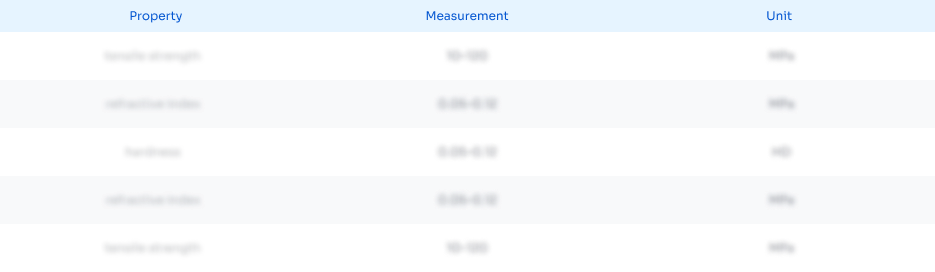
Abstract
Description
Claims
Application Information

- R&D Engineer
- R&D Manager
- IP Professional
- Industry Leading Data Capabilities
- Powerful AI technology
- Patent DNA Extraction
Browse by: Latest US Patents, China's latest patents, Technical Efficacy Thesaurus, Application Domain, Technology Topic, Popular Technical Reports.
© 2024 PatSnap. All rights reserved.Legal|Privacy policy|Modern Slavery Act Transparency Statement|Sitemap|About US| Contact US: help@patsnap.com