Composite catalyst for preparing aromatic polycarbonate and application of composite catalyst
A composite catalyst and polycarbonate technology, which is applied in the field of composite catalysts for the preparation of aromatic polycarbonates, can solve problems such as branching, local overheating, difficult to control, rearrangement, etc., to reduce production costs, reduce equipment requirements, and process stability Effect
- Summary
- Abstract
- Description
- Claims
- Application Information
AI Technical Summary
Problems solved by technology
Method used
Image
Examples
preparation example Construction
[0030] In addition, for the composite catalyst of the present invention, the present invention specially designs a preparation method, which includes the following steps: uniformly mixing the organic base compound and the basic ionic liquid to obtain the composite catalyst.
[0031] In addition, the composite catalyst provided by the invention is applied in the preparation process of aromatic polycarbonate, including the following steps:
[0032] Polycarbonate was synthesized by non-phosgene method using dihydroxy compound and carbonic diester as raw materials. Among them, the molar ratio of dihydroxy compound to diester carbonate is 1: (1.015~1.1), and the molar ratio of composite catalyst to dihydroxy compound is (0.005~0.05):1; the synthesis process of polycarbonate includes transesterification process and Polycondensation process: The specific process of transesterification is: the reaction temperature is 130-190 °C, the pressure is reduced, the reaction time is 2-5 hours,...
Embodiment 1
[0036] The invention provides a kind of composite catalyst, and raw material component comprises tert-butyllithium and alkaline ionic liquid, wherein, R 1 is isopropyl, R 2 is dimethylamino, X - for CH3COO - .
[0037] Adopt the composite catalyst in the present embodiment to prepare aromatic polycarbonate, comprise the following steps:
[0038] S101: mix 1mol tert-butyllithium with 3mol alkaline ionic liquid (R 1 is isopropyl, R 2 is dimethylamino, X - for CH 3 COO - ) are mixed and dispersed in an organic solvent to obtain a composite catalyst.
[0039] S102: Mix diphenyl carbonate and bisphenol A at a molar ratio of 1.015:1, and then heat to a molten state;
[0040] S103: Add the composite catalyst to the product obtained in S102 at 0.5 wt% relative to the mass of bisphenol A to carry out transesterification reaction, and react for 2 hours at a temperature of 150°C and a pressure of 3000Pa to obtain a prepolymer; then raise the temperature to 170 ℃, the pressure dro...
Embodiment 2
[0046] The invention provides a kind of composite catalyst, and raw material component comprises tert-butyllithium and alkaline ionic liquid, wherein, R 1 is ethyl, R 2 is amino, X - for CH3COO - .
[0047] Adopt the composite catalyst in the present embodiment to prepare aromatic polycarbonate, comprise the following steps:
[0048] S101: mix 1mol tert-butyllithium with 5mol alkaline ionic liquid (R1 is ethyl, R2 is amino, X - for CH 3 COO - ) are mixed and dispersed in an organic solvent to obtain a composite catalyst.
[0049] S102: mixing diphenyl carbonate and bisphenol A in a molar ratio of 1.05:1, and then heating to a molten state;
[0050] S103: Add the composite catalyst to the product obtained in S102 at 5 wt% relative to the mass of bisphenol A to carry out transesterification reaction, and react for 2 hours at a temperature of 150°C and a pressure of 3000Pa to obtain a prepolymer; then raise the temperature to 190°C , the pressure dropped to 1500Pa, reacte...
PUM
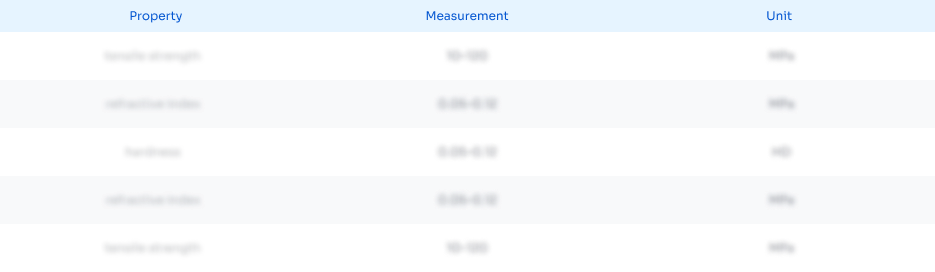
Abstract
Description
Claims
Application Information

- R&D
- Intellectual Property
- Life Sciences
- Materials
- Tech Scout
- Unparalleled Data Quality
- Higher Quality Content
- 60% Fewer Hallucinations
Browse by: Latest US Patents, China's latest patents, Technical Efficacy Thesaurus, Application Domain, Technology Topic, Popular Technical Reports.
© 2025 PatSnap. All rights reserved.Legal|Privacy policy|Modern Slavery Act Transparency Statement|Sitemap|About US| Contact US: help@patsnap.com