Automobile plastic backrest material and preparation method thereof
A technology of plastic and backrest, which is applied to the material of automobile plastic backrest and its preparation field, can solve the problems of high density, low surface finish, affecting lifespan, etc., and achieves the effect of high finish, high structural strength and improved stability.
- Summary
- Abstract
- Description
- Claims
- Application Information
AI Technical Summary
Problems solved by technology
Method used
Image
Examples
Embodiment 1
[0017] A material for an automobile plastic backrest, made of the following materials in parts by weight, including 55 parts of polystyrene, 26 parts of polyethylene terephthalate, 20 parts of polyphenylene ether, and 8 parts of polyoxymethylene resin 5 parts of sodium silicate, 13 parts of dimethylformamide, 4 parts of triethanolamine, 5 parts of methyl acetate, 11 parts of carbon black, 17 parts of dichlorodifluoromethane, 24 parts of sodium fatty alcohol polyoxyethylene ether sulfate , 23 parts of silicate, 7 parts of fluorine oil, 13 parts of polyoxyethylene polyoxypropanolamine ether, 14 parts of triphenyl antimony dichloride, 16 parts of aluminum stearate, 8 parts of aluminum borate whiskers, bismuth oxide 16 parts and sodium alkylsulfonate 8 parts.
[0018] A preparation method of a material for an automobile plastic backrest, comprising the following steps:
[0019] 1) 55 parts of polystyrene, 26 parts of polyethylene terephthalate, 20 parts of polyphenylene ether, 8 ...
Embodiment 2
[0024] A material for the plastic backrest of an automobile, made of the following materials in parts by weight, including 56.5 parts of polystyrene, 28.5 parts of polyethylene terephthalate, 22.5 parts of polyphenylene ether, and 11 parts of polyoxymethylene resin 7.5 parts of sodium silicate, 15 parts of dimethylformamide, 6 parts of triethanolamine, 7 parts of methyl acetate, 13.5 parts of carbon black, 18.5 parts of dichlorodifluoromethane, 26 parts of fatty alcohol polyoxyethylene ether sodium sulfate , 24.5 parts of silicate, 10.5 parts of fluorine oil, 14 parts of polyoxyethylene polyoxypropanolamine ether, 16 parts of triphenylantimony dichloride, 18 parts of aluminum stearate, 10 parts of aluminum borate whiskers, bismuth oxide 18 parts and sodium alkylsulfonate 10.5 parts.
[0025] A preparation method of a material for an automobile plastic backrest, comprising the following steps:
[0026] 1) 56.5 parts of polystyrene, 28.5 parts of polyethylene terephthalate, 22....
Embodiment 3
[0031]A material for the plastic backrest of an automobile, made of the following materials in parts by weight, including 58 parts of polystyrene, 31 parts of polyethylene terephthalate, 25 parts of polyphenylene ether, and 14 parts of polyoxymethylene resin 10 parts of sodium silicate, 17 parts of dimethylformamide, 8 parts of triethanolamine, 9 parts of methyl acetate, 16 parts of carbon black, 20 parts of dichlorodifluoromethane, 28 parts of sodium fatty alcohol polyoxyethylene ether sulfate , 26 parts of silicate, 14 parts of fluorine oil, 15 parts of polyoxyethylene polyoxypropanolamine ether, 18 parts of triphenylantimony dichloride, 20 parts of aluminum stearate, 12 parts of aluminum borate whiskers, bismuth oxide 20 parts and sodium alkylsulfonate 13 parts.
[0032] A preparation method of a material for an automobile plastic backrest, comprising the following steps:
[0033] 1) 58 parts of polystyrene, 31 parts of polyethylene terephthalate, 25 parts of polyphenylene...
PUM
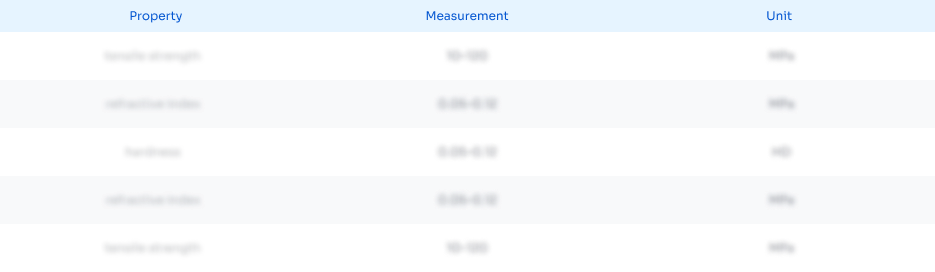
Abstract
Description
Claims
Application Information

- R&D
- Intellectual Property
- Life Sciences
- Materials
- Tech Scout
- Unparalleled Data Quality
- Higher Quality Content
- 60% Fewer Hallucinations
Browse by: Latest US Patents, China's latest patents, Technical Efficacy Thesaurus, Application Domain, Technology Topic, Popular Technical Reports.
© 2025 PatSnap. All rights reserved.Legal|Privacy policy|Modern Slavery Act Transparency Statement|Sitemap|About US| Contact US: help@patsnap.com