Welding machine with wire feeding and wire drawing being conducted alternately and power supply control method thereof
A welding machine power supply and control method technology, applied in manufacturing tools, welding equipment, arc welding equipment and other directions, can solve the problems of difficulty in welding thin plates and spatter, and achieve the effect of reducing arc heat and spatter
- Summary
- Abstract
- Description
- Claims
- Application Information
AI Technical Summary
Problems solved by technology
Method used
Image
Examples
Embodiment 1
[0260] In this embodiment, VV and CC adopt image 3 Existing circuit modules in ;
[0261] Such as Figure 4 with Image 6 As shown, W0, W1, W2, W3, W4, W5, W6, W7, W8, W9, W10, W11 are potentiometers, U1, U2 are operational amplifiers 353, U3A is D flip-flop 4013, U4, U5 are single Steady-state flip-flop 4538;
[0262] A welding machine that alternately feeds and draws wire, adopts an analog control circuit, such as Image 6 As shown, one end of the potentiometer W0, W1, W2, W3, W4, W5, W6, W7, W8, W9, W10, W11 is connected to the power supply VCC, W0, W1, W2, W3, W4, W5, W6, W7, W10 , The other end of W11 is grounded, one end of resistors R1, R2, R3, and capacitor C1 is grounded, the middle end of W0 is connected to pin 1 of K6, the middle end of W1 is connected to pin 2 of K3, the middle end of W2 is connected to pin 1 of K3, and the middle end of W3 is connected to K2 The middle end of W4 is connected with pin 2 of K6, the middle end of W5 is connected with pin 5 of U...
Embodiment 2
[0277] A control method for a welding machine that alternately feeds and draws wire is basically the same as in Embodiment 1, the difference is that in step 4, D and F are connected, and the arc voltage reset mode ends the wire drawing stage and starts the next step Arcing stage: after Uh rises to a certain value, U2-1 becomes high, contact D is connected to contact F, the high level is sent to contact D through diode D4, U3 resets, U3-1 is low, and the wire feeder rotates forward , wire feeding, K1-15 is connected with K1-2, so that Uv is connected with Iin, and the arcing stage of stage 1 is repeatedly entered.
Embodiment 3
[0279] A control method for a welding machine that alternately feeds and draws wire, which is basically the same as Embodiment 1, the difference is that in step 4, the timing of the end of the retraction is reset by delay reset mode and arc voltage reset after the short circuit occurs The method is combined to end the spinning stage and start the next arcing stage;
[0280] Contact D is connected to contact E, and contact D is connected to contact F. "Delayed reset mode" and "arc voltage reset mode" exist at the same time, U4-7 first becomes high, which is "delayed reset mode"; U2-1 first changes High, for "arc voltage reset mode".
PUM
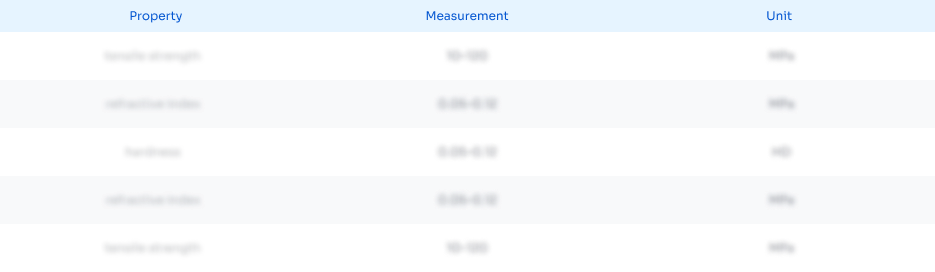
Abstract
Description
Claims
Application Information

- R&D Engineer
- R&D Manager
- IP Professional
- Industry Leading Data Capabilities
- Powerful AI technology
- Patent DNA Extraction
Browse by: Latest US Patents, China's latest patents, Technical Efficacy Thesaurus, Application Domain, Technology Topic, Popular Technical Reports.
© 2024 PatSnap. All rights reserved.Legal|Privacy policy|Modern Slavery Act Transparency Statement|Sitemap|About US| Contact US: help@patsnap.com