Rosin furan preservative for dipping cotton wood and preparation method and application thereof
A preservative and furan technology, applied in the field of rosin furan preservative and its preparation, can solve the problems of environmental pollution of impregnating liquid, long processing route, lack of technical methods, etc., and achieves good anti-corrosion effect, good loss resistance and raw material source. wide effect
- Summary
- Abstract
- Description
- Claims
- Application Information
AI Technical Summary
Problems solved by technology
Method used
Image
Examples
Embodiment 1
[0018] (1) Collect 20 parts of rosin and 100 parts of absolute ethanol from Pine massoniana, and stir in a water bath at a temperature of 40° C. until a uniform rosin solution is obtained, which is a pine resin alcohol solution.
[0019] (2) Hydrolyze 1,4-dichlorobutene in sodium hydroxide solution to generate butenediol at 110°C, centrifuge to remove sodium chloride, concentrate the filtrate in an evaporative crystallizer, and separate alkali metal carboxylic acid Salt, and high boilers are removed in a distillation column. Feed the refined butylene glycol into the reactor, use nickel as the catalyst, and hydrogenate the butylene glycol to generate butylene glycol at 80-120°C and a certain pressure, enter the ring-closure reactor after distillation, And 120 ~ 140 ℃ in acidic medium to generate crude tetrahydrofuran, distilled dehydration and off high boilers, and finally distilled to obtain high-purity tetrahydrofuran.
[0020] (3) Add 20 parts of high-purity tetrahydrofuran...
Embodiment 2
[0022] (1) Collect 30 parts of rosin and 200 parts of absolute ethanol from Yunnan pine, and stir in a water bath at a temperature of 40° C. until a uniform rosin solution is obtained, which is a pine resin alcohol solution.
[0023] (2) Hydrolyze 1,4-dichlorobutene in sodium hydroxide solution to generate butenediol at 110°C, centrifuge to remove sodium chloride, concentrate the filtrate in an evaporative crystallizer, and separate alkali metal carboxylic acid Salt, and high boilers are removed in a distillation column. Feed the refined butylene glycol into the reactor, use nickel as the catalyst, and hydrogenate the butylene glycol to generate butylene glycol at 80-120°C and a certain pressure, enter the ring-closure reactor after distillation, And 120 ~ 140 ℃ in acidic medium to generate crude tetrahydrofuran, distilled dehydration and off high boilers, and finally distilled to obtain high-purity tetrahydrofuran.
[0024] (3) Add 30 parts of high-purity tetrahydrofuran to ...
Embodiment 3
[0026] (1) Collect 25 parts of rosin and 150 parts of absolute ethanol from the southern Asian pine, and stir in a water bath at a temperature of 40° C. until a uniform rosin solution is obtained, which is a pinoresin alcohol solution.
[0027] (2) Hydrolyze 1,4-dichlorobutene in sodium hydroxide solution to generate butenediol at 110°C, centrifuge to remove sodium chloride, concentrate the filtrate in an evaporative crystallizer, and separate alkali metal carboxylic acid Salt, and high boilers are removed in a distillation column. Feed the refined butylene glycol into the reactor, use nickel as the catalyst, and hydrogenate the butylene glycol to generate butylene glycol at 80-120°C and a certain pressure, enter the ring-closure reactor after distillation, And 120 ~ 140 ℃ in acidic medium to generate crude tetrahydrofuran, distilled dehydration and off high boilers, and finally distilled to obtain high-purity tetrahydrofuran.
[0028] (3) Add 25 parts of high-purity tetrahyd...
PUM
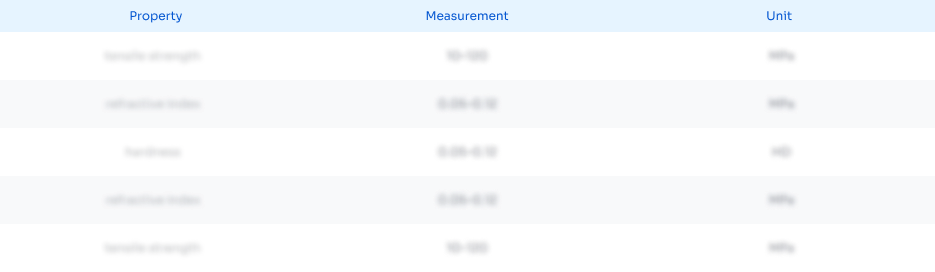
Abstract
Description
Claims
Application Information

- R&D Engineer
- R&D Manager
- IP Professional
- Industry Leading Data Capabilities
- Powerful AI technology
- Patent DNA Extraction
Browse by: Latest US Patents, China's latest patents, Technical Efficacy Thesaurus, Application Domain, Technology Topic, Popular Technical Reports.
© 2024 PatSnap. All rights reserved.Legal|Privacy policy|Modern Slavery Act Transparency Statement|Sitemap|About US| Contact US: help@patsnap.com