Manufacture method for subsided high-density mutual connection board
A manufacturing method and technology of flexible boards, which are applied in multilayer circuit manufacturing, printed circuit manufacturing, printed circuit and other directions, can solve the problems of unsatisfactory fineness, inability to etch, difficult to etch, etc. The effect of dimensional stability and improved bonding force
- Summary
- Abstract
- Description
- Claims
- Application Information
AI Technical Summary
Problems solved by technology
Method used
Image
Examples
Embodiment Construction
[0034] The present invention will be further described in detail below in conjunction with the accompanying drawings and embodiments.
[0035] Such as Figure 1-10 as shown,
[0036] The manufacturing method of the rigid-flex circuit board of the present embodiment, its technological process is:
[0037] Normal production of inner soft board 4—conduction copper pillar 2 electroplating—insulation adhesive layer 3 lamination—insulation adhesive layer 3 grinding—outer hard board 1 circuit formation (additive electroplating process)—— Subsidence area 6 processing - steel plate 5 processing
[0038] Specifically include the following steps:
[0039] 1) Make the inner soft board 4 (such as figure 2 ), the inner flexible board 4 is produced by conventional methods, specifically including: first cutting the inner soft board 4, drilling and electroplating conduction, the drilling can be mechanical drilling or laser drilling, and then the inner layer Etching of 4 lines on the flex...
PUM
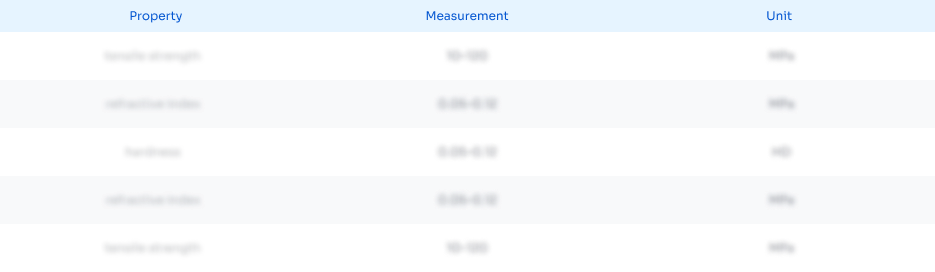
Abstract
Description
Claims
Application Information

- R&D
- Intellectual Property
- Life Sciences
- Materials
- Tech Scout
- Unparalleled Data Quality
- Higher Quality Content
- 60% Fewer Hallucinations
Browse by: Latest US Patents, China's latest patents, Technical Efficacy Thesaurus, Application Domain, Technology Topic, Popular Technical Reports.
© 2025 PatSnap. All rights reserved.Legal|Privacy policy|Modern Slavery Act Transparency Statement|Sitemap|About US| Contact US: help@patsnap.com