Super toughness MC nylon material and preparation method thereof
A nylon and super-tough technology is applied in the field of super-tough MC nylon material and its preparation. dispersive effect
- Summary
- Abstract
- Description
- Claims
- Application Information
AI Technical Summary
Problems solved by technology
Method used
Image
Examples
Embodiment 1
[0019] Add 100 parts of caprolactam into the Erlenmeyer flask, place it in an oil bath and raise the temperature to 90°C to heat the caprolactam to melt. Raise the temperature of the system to 120°C, vacuumize and dehydrate under the condition of magnetic stirring, release the vacuum when large bubbles appear; continue to stir and add 0.35 parts of sodium hydroxide to vacuumize, while raising the temperature of the system to 140°C, continue to stir and dehydrate, large bubbles appear, and continue to pump Vacuum for 10 minutes, release the vacuum; continue to stir, add 0.75 parts of toluene diisocyanate to obtain a prepolymerization system, cast it into a mold preheated in an oven at 180 ° C, continue heating for 2 hours, cool to room temperature, and obtain MC nylon Materials and test results are shown in Table 1.
Embodiment 2
[0021] Add 100 parts of caprolactam into the Erlenmeyer flask, place it in an oil bath and heat up to 90°C to heat the caprolactam to melt. After the caprolactam is melted, add 0.05 parts of modified nano-silica, and stir to make it completely dissolve in the caprolactam melt. . Raise the temperature of the system to 120°C, vacuumize and dehydrate under the condition of magnetic stirring, release the vacuum when large bubbles appear; continue to stir and add 0.35 parts of sodium hydroxide to vacuumize, while raising the temperature of the system to 140°C, continue to stir and dehydrate, large bubbles appear, and continue to pump Vacuum for 10 minutes, release the vacuum; continue to stir, add 0.75 parts of toluene diisocyanate to obtain a prepolymerization system, cast it into a mold preheated in an oven at 180 ° C, continue heating for 2 hours, cool to room temperature, and obtain MC nylon Materials and test results are shown in Table 1.
Embodiment 3
[0023] Add 100 parts of caprolactam into the Erlenmeyer flask, place it in an oil bath and heat up to 90°C to heat the caprolactam to melt. After the caprolactam is melted, add 0.1 part of modified nano-silica, stir to make it completely dissolve in the caprolactam melt . Raise the temperature of the system to 120°C, vacuumize and dehydrate under the condition of magnetic stirring, release the vacuum when large bubbles appear; continue to stir and add 0.35 parts of sodium hydroxide to vacuumize, while raising the temperature of the system to 140°C, continue to stir and dehydrate, large bubbles appear, and continue to pump Vacuum for 10 minutes, release the vacuum; continue to stir, add 0.75 parts of toluene diisocyanate to obtain a prepolymerization system, cast it into a mold preheated in an oven at 180 ° C, continue heating for 2 hours, cool to room temperature, and obtain MC nylon Materials and test results are shown in Table 1.
PUM
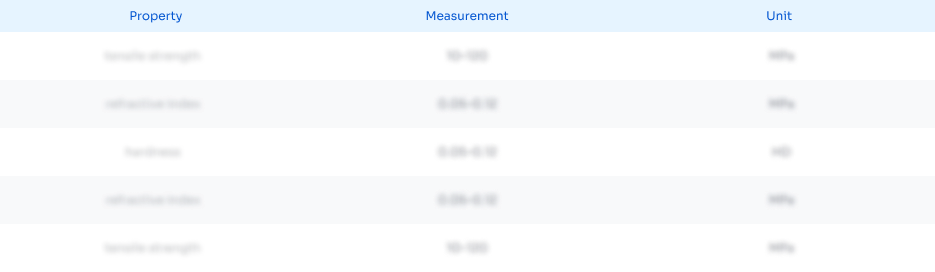
Abstract
Description
Claims
Application Information

- R&D
- Intellectual Property
- Life Sciences
- Materials
- Tech Scout
- Unparalleled Data Quality
- Higher Quality Content
- 60% Fewer Hallucinations
Browse by: Latest US Patents, China's latest patents, Technical Efficacy Thesaurus, Application Domain, Technology Topic, Popular Technical Reports.
© 2025 PatSnap. All rights reserved.Legal|Privacy policy|Modern Slavery Act Transparency Statement|Sitemap|About US| Contact US: help@patsnap.com