Preparation method of MAX-phase-imitating accident fault-tolerant nuclear fuel pellet
A nuclear fuel and accident technology, applied in fuel elements, nuclear power generation, climate sustainability, etc., can solve the problems of nuclear power plant safety hazards, fission gas release, steep temperature gradient of fuel pellets, etc., to achieve process stability improvement and cost reduction Effect
- Summary
- Abstract
- Description
- Claims
- Application Information
AI Technical Summary
Problems solved by technology
Method used
Image
Examples
example 1
[0025] (1) Take the following raw materials in mass percentage: 40 μm uranium dioxide 70wt.%, 20 μm silicon 12wt.%, 20 μm graphite powder 12wt.%, zinc stearate 0.1wt.%, 10 μm TiO 2 5.9wt.%; after wet mixing the above powder in ethanol for 24 hours, take out the powder after drying;
[0026] (2) Prepare U by hot pressing sintering process 3 Si 2 C 2 : Put the powder in a graphite mold and vacuumize to 1.0×10 -3 Pa, the temperature is raised to 1300°C at 20°C / min, and then a pressure of 100MPa is applied and kept for 4 hours to obtain U 3 Si 2 C 2 ;
[0027] (3) Processing and forming: to be U 3 Si 2 C 2 After cooling, it is taken out and processed to the required shape and size, which is the fault-tolerant nuclear fuel pellet imitating the MAX phase.
[0028] U prepared by this method 3 Si 2 C 2 The density is 93.5%.
example 2
[0030] (1) Take the following raw materials in mass percentage: 20μm uranium dioxide 85wt.%, 5μm silicon carbide 7wt.%, 5μm flake graphite 7wt.%, zinc stearate 0.1wt.%, 1μm TiO 2 0.9wt.%; after wet mixing the above powder in ethanol for 12 hours, take out the powder after drying;
[0031] (2) Prepare U by hot pressing sintering process 3 Si 2 C 2 : Put the powder in a graphite mold and vacuumize to 1.1×10 -3 Pa, the temperature is raised to 1600°C at 5°C / min, and then a pressure of 20MPa is applied and kept for 4 hours to obtain U 3 Si 2 C 2 ;
[0032] (3) Processing and forming: to be U 3 Si 2 C 2 After cooling, it is taken out and processed to the required shape and size, which is the fault-tolerant nuclear fuel pellet imitating the MAX phase.
[0033] U prepared by this method 3 Si 2 C 2 The density is 97.3%.
example 3
[0035] (1) Take the following raw materials by mass percentage: 30 μm uranium dioxide 80wt.%, 10 μm silicon carbide 8wt.%, 10 μm carbon black 8wt.%, zinc stearate 0.1wt.%, 5 μm TiO 2 3.9wt.%; after wet mixing the above powder in ethanol for 18 hours, take out the powder after drying;
[0036] (2) Prepare U by hot pressing sintering process 3 Si 2 C 2 : Put the powder in a graphite mold and vacuumize to 0.9×10 -3 Pa, the temperature is raised to 1450°C at 10°C / min, and then a pressure of 60MPa is applied and kept for 2 hours to obtain U 3 Si 2 C 2 ;
[0037] (3) Processing and forming: to be U 3 Si 2 C 2 After cooling, it is taken out and processed to the required shape and size, which is the fault-tolerant nuclear fuel pellet imitating the MAX phase.
[0038] U prepared by this method 3 Si 2 C 2 The density is 95.1%.
PUM
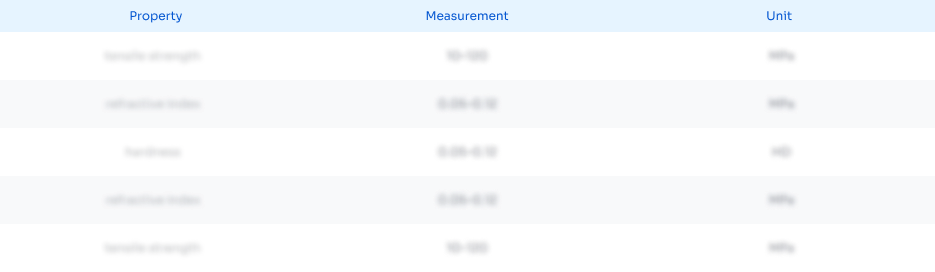
Abstract
Description
Claims
Application Information

- R&D
- Intellectual Property
- Life Sciences
- Materials
- Tech Scout
- Unparalleled Data Quality
- Higher Quality Content
- 60% Fewer Hallucinations
Browse by: Latest US Patents, China's latest patents, Technical Efficacy Thesaurus, Application Domain, Technology Topic, Popular Technical Reports.
© 2025 PatSnap. All rights reserved.Legal|Privacy policy|Modern Slavery Act Transparency Statement|Sitemap|About US| Contact US: help@patsnap.com