Preparation process of high-toughness tencel fibers for clothes
A Tencel fiber and preparation technology, applied in the fiber field, can solve the problems of limited fiber strength, organic solvent residue, environmental pollution, etc., and achieve the effects of increased anti-wrinkle ability, improved fiber toughness, and simple operation process
- Summary
- Abstract
- Description
- Claims
- Application Information
AI Technical Summary
Problems solved by technology
Method used
Examples
Embodiment 1
[0026] A preparation process for high-tenacity tencel fibers for clothing, characterized in that the preparation of the fibers comprises steps as follows:
[0027] (1) Using logs as raw materials for fiber preparation, crushing them to obtain shredded wood, soaking in 3% sodium hydroxide aqueous solution for 3 hours, dissolving the cellulose in the wood, and obtaining an alkali cellulose solution after filtration;
[0028] (2) Expose the alkali cellulose solution to the air, and place it at 30°C for 2 hours, so that the fiber undergoes oxidative degradation, and the degree of polymerization drops to the process requirement, add 4% carbon disulfide, and keep it warm at 50°C for 30 minutes Finally, obtain the cellulose xanthate solution, utilize 2% sulfuric acid solution to separate out the cellulose, and prepare pure wood cellulose pulp;
[0029] (3) Use negative pressure suction to reduce the boiling point of water in lignocellulosic pulp to 80-85°C, and reduce the moisture co...
Embodiment 2
[0033] A preparation process for high-tenacity tencel fibers for clothing, characterized in that the preparation of the fibers comprises steps as follows:
[0034] (1) Use logs as raw materials for fiber preparation, crush and squeeze to obtain wood chips, soak in 6% sodium hydroxide aqueous solution for 1 hour, dissolve the cellulose in the wood, and obtain an alkali cellulose solution after filtration;
[0035] (2) Expose the alkali cellulose solution to the air, and place it at 35°C for 2 hours, so that the fiber undergoes oxidative degradation, and the degree of polymerization drops to the process requirement, add 2% carbon disulfide, and keep it warm at 60°C for 60 minutes Finally, obtain the cellulose xanthate solution, utilize 3% sulfuric acid solution to separate out the cellulose, and prepare pure wood cellulose pulp;
[0036] (3) Use negative pressure suction to reduce the boiling point of water in lignocellulosic pulp to 80-85°C, and reduce the moisture content of l...
Embodiment 3
[0040] A preparation process for high-tenacity tencel fibers for clothing, characterized in that the preparation of the fibers comprises steps as follows:
[0041] (1) Use logs as the raw material for fiber preparation, squeeze and pulverize to obtain wood chips, soak in 5% sodium hydroxide aqueous solution for 1.5 hours, dissolve the cellulose in the wood, and obtain alkali cellulose solution after filtration;
[0042] (2) Expose the alkali cellulose solution to the air, and place it at 40°C for 1 hour, so that the fiber undergoes oxidative degradation, and the degree of polymerization drops to the process requirement, add 3% carbon disulfide, and keep it warm at 50°C for 30 minutes Finally, obtain the cellulose xanthate solution, utilize 3% sulfuric acid solution to separate out the cellulose, and prepare pure wood cellulose pulp;
[0043] (3) Use negative pressure suction to reduce the boiling point of water in lignocellulosic pulp to 80-85°C, and reduce the moisture conten...
PUM
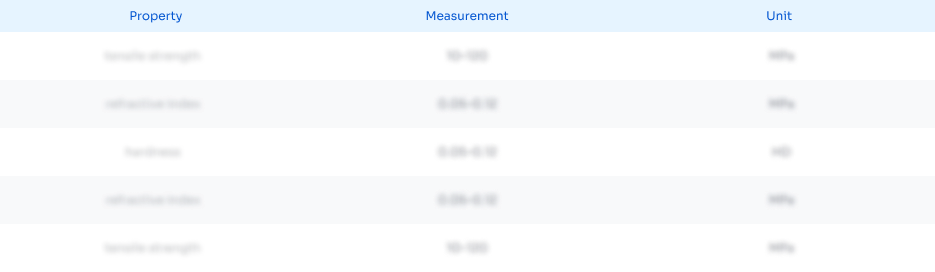
Abstract
Description
Claims
Application Information

- R&D
- Intellectual Property
- Life Sciences
- Materials
- Tech Scout
- Unparalleled Data Quality
- Higher Quality Content
- 60% Fewer Hallucinations
Browse by: Latest US Patents, China's latest patents, Technical Efficacy Thesaurus, Application Domain, Technology Topic, Popular Technical Reports.
© 2025 PatSnap. All rights reserved.Legal|Privacy policy|Modern Slavery Act Transparency Statement|Sitemap|About US| Contact US: help@patsnap.com