Coarse gold refining method
A crude gold and filter residue technology, which is applied in the field of metallurgy, can solve problems such as insufficient product purity, high pyromelting temperature, and complicated process flow, and achieve the effects of lower gold content requirements, fewer production steps, and simple methods and operations
- Summary
- Abstract
- Description
- Claims
- Application Information
AI Technical Summary
Problems solved by technology
Method used
Examples
Embodiment 1
[0032] The percentage content of each component of crude gold is: gold 70.35%, silver 20.05%, copper 3.32%, iron 3.19%, antimony 1.64%, silicon 1.35%. The implementation steps are as follows:
[0033] (1) Weigh 50.4879g of crude gold powder, add 100mL of 20% nitric acid solution, put it on an electric stove for 2 hours, filter, wash the filter residue I with deionized water three times, and the wet weight of the filter residue is 39.3214g.
[0034] (2) Add 16 g of potassium nitrate to the filter residue I obtained in step (1), mix well, and send it to a muffle furnace for 1.5 hours of roasting at a roasting temperature of 600°C.
[0035] (3) The calcined residue obtained in step (2) was added to 80 mL of 25% potassium hydroxide solution for immersion for 1 hour, filtered, and the filter residue II was washed with deionized water for 3 times.
[0036] (4) The filter residue II obtained in step (3) was added to 80 mL of 15% nitric acid solution for immersion for 1 hour, filtere...
Embodiment 2
[0040]The composition of coarse gold powder is: gold 70.35%, silver 20.05%, copper 3.32%, iron 3.19%, antimony 1.64%, silicon 1.35%. The implementation steps are as follows:
[0041] (1) Weigh 50.3245g of crude gold powder, add 100mL of 20% nitric acid solution by mass, put it on an electric furnace to cook for 1 hour, filter, and wash the filter residue I with deionized water for 3 times, and the wet weight of the filter residue is 38.3214g.
[0042] (2) Add 16 g of potassium nitrate to the filter residue I obtained in step (1), mix well, and send it to a muffle furnace for roasting for 2 hours at a roasting temperature of 500°C.
[0043] (3) The mass fraction of the roasting slag obtained in step (2) is 5%
[0044] Dig with 200 mL of potassium hydroxide solution for 1 h, filter, and wash the filter residue II with deionized water 3 times.
[0045] (4) The filter residue II obtained in step (3) was added with 110 mL of a 15% nitric acid solution to digest for 1 hour, filter...
Embodiment 3
[0049] The composition of coarse gold powder is: gold 81.15%, silver 11.27%, copper 2.37%, iron 2.08%, antimony 1.70%, silicon 1.43%. The implementation steps are as follows:
[0050] (1) Weigh 50.5064g of crude gold powder, add 45mL of 30% nitric acid solution by mass, put it on an electric furnace to immerse for 1 hour, filter, and wash the filter residue I with deionized water for 3 times, and the wet weight of the filter residue is 39.5324g.
[0051] (2) Add 8 g of potassium nitrate to the filter residue I obtained in step (1), mix well, and send it to a muffle furnace for calcination for 1.5 hours at a calcination temperature of 500°C.
[0052] (3) The roasting residue obtained in step (2) was added with 45 mL of potassium hydroxide solution with a mass fraction of 30% to be digested for 1 hour, filtered, and the filter residue II was washed three times with deionized water.
[0053] (4) The filter residue II obtained in step (3) was added with 45 mL of 30% nitric acid s...
PUM
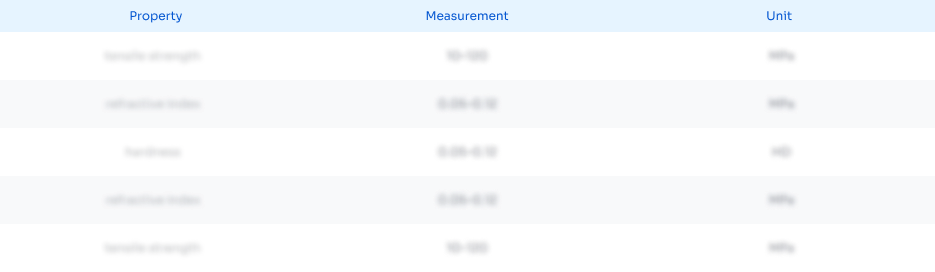
Abstract
Description
Claims
Application Information

- R&D
- Intellectual Property
- Life Sciences
- Materials
- Tech Scout
- Unparalleled Data Quality
- Higher Quality Content
- 60% Fewer Hallucinations
Browse by: Latest US Patents, China's latest patents, Technical Efficacy Thesaurus, Application Domain, Technology Topic, Popular Technical Reports.
© 2025 PatSnap. All rights reserved.Legal|Privacy policy|Modern Slavery Act Transparency Statement|Sitemap|About US| Contact US: help@patsnap.com