Sub-molten salt method for totally recycling vanadium, tungsten and titanium from waste denitration catalyst
A technology of denitrification catalyst and sub-molten salt, which is applied in the fields of tungsten, titanium and vanadium recovery, can solve the problems of energy consumption and element waste, achieve low production cost, huge economic and social benefits, and relieve resource pressure.
- Summary
- Abstract
- Description
- Claims
- Application Information
AI Technical Summary
Problems solved by technology
Method used
Image
Examples
Embodiment 1
[0019] The waste denitrification catalyst is subjected to soot blowing and grinding treatment to obtain waste denitration catalyst powder; the waste denitration catalyst powder is leached with sodium hydroxide sub-molten salt leaching solution, the concentration of sodium hydroxide sub-molten salt in the leaching solution is 5mol / L, and the solid-liquid ratio is 1g: 40ml, the leaching temperature is 130°C, and the leaching time is 4h, to obtain the leaching solution and leaching residue; the leaching residue is cleaned and filtered with hydrochloric acid to obtain anatase titanium dioxide and cleaning solution, and the cleaning solution is evaporated and crystallized to obtain NaCl; the leaching solution is Continue to mix with sodium hydroxide sub-molten salt to carry out sub-molten salt leaching behavior, and recycle the leachate until the tungsten content in the solution reaches 5%, stop the circulation; Calcium is calcified and precipitated, first adding hydrochloric acid t...
Embodiment 2
[0021] The waste denitration catalyst is soot blown and ground to obtain the waste denitration catalyst powder; the waste denitration catalyst powder is leached with the sodium hydroxide sub-molten salt leaching solution, the concentration of the sodium hydroxide sub-molten salt in the leaching solution is 10mol / L, and the solid-to-liquid ratio is 1g: 100ml, the leaching temperature is 180°C, and the leaching time is 8h, to obtain the leaching solution and leaching residue; the leaching residue is cleaned and filtered with hydrochloric acid to obtain anatase titanium dioxide and cleaning solution, and the cleaning solution is evaporated and crystallized to obtain NaCl; the leaching solution is Continue to mix with sodium hydroxide sub-molten salt to carry out sub-molten salt leaching behavior, and recycle the leachate until the tungsten content in the solution reaches 10%, stop the circulation; Calcium is calcified and precipitated, first adding hydrochloric acid to the solutio...
Embodiment 3
[0023] The waste denitration catalyst is subjected to soot blowing and grinding to obtain the waste denitration catalyst powder; the waste denitration catalyst powder is leached with the sodium hydroxide sub-molten salt leaching solution, the concentration of the sodium hydroxide sub-molten salt in the leaching solution is 6mol / L, and the solid-to-liquid ratio is 1g: 50ml, the leaching temperature is 140°C, and the leaching time is 5h, to obtain the leaching solution and leaching residue; the leaching residue is cleaned and filtered with hydrochloric acid to obtain anatase titanium dioxide and cleaning solution, and the cleaning solution is evaporated and crystallized to obtain NaCl; the leaching solution is Continue to mix with sodium hydroxide sub-molten salt to carry out sub-molten salt leaching behavior, and recycle the leach solution until the tungsten content in the solution reaches 6%, stop the circulation; add hydrochloric acid and chloride to the leach solution with a m...
PUM
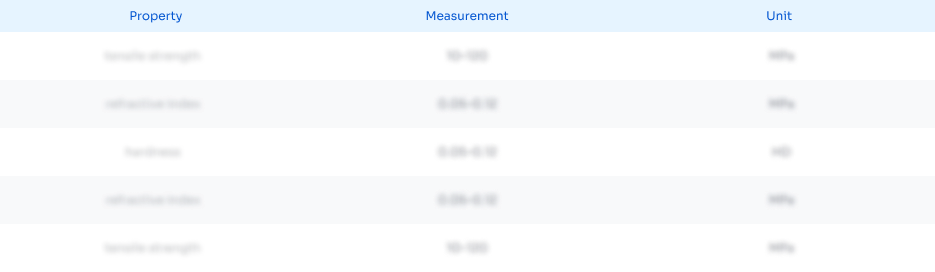
Abstract
Description
Claims
Application Information

- Generate Ideas
- Intellectual Property
- Life Sciences
- Materials
- Tech Scout
- Unparalleled Data Quality
- Higher Quality Content
- 60% Fewer Hallucinations
Browse by: Latest US Patents, China's latest patents, Technical Efficacy Thesaurus, Application Domain, Technology Topic, Popular Technical Reports.
© 2025 PatSnap. All rights reserved.Legal|Privacy policy|Modern Slavery Act Transparency Statement|Sitemap|About US| Contact US: help@patsnap.com