EtherCAT-based direct current common bus servo driving apparatus
A servo drive device and servo drive technology, applied in the field of servo drive, can solve the problems of multi-axis synchronization of the motion system, lack of real-time performance, high unit price of CAN field bus components, high comprehensive cost of the control system, etc., to solve related fault delays, topology Convenient structure and strong real-time effects
- Summary
- Abstract
- Description
- Claims
- Application Information
AI Technical Summary
Problems solved by technology
Method used
Image
Examples
Embodiment Construction
[0023] The principles and features of the present invention are described below in conjunction with the accompanying drawings, and the examples given are only used to explain the present invention, and are not intended to limit the scope of the present invention.
[0024] Such as figure 1 As shown, a DC common bus servo drive device based on EtherCAT, the DC common bus servo drive device includes: servo drive assembly 1, servo motor assembly 2, control unit 3 and rectifier unit 4, rectifier unit 4 and control unit 3 are connected Servo drive assembly 1, the servo drive assembly 1 is connected to the servo motor assembly 2;
[0025] The control unit 3 includes an EtherCAT master module 31, the EtherCAT master module 31 is connected to the servo drive assembly 1, and the EtherCAT master module 31 is used to control the servo drive assembly 1;
[0026] The servo drive assembly 1 includes at least one servo drive unit 11 connected in sequence, the servo motor assembly 2 includes ...
PUM
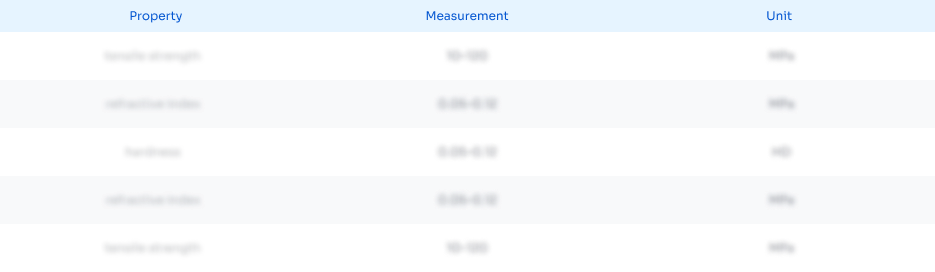
Abstract
Description
Claims
Application Information

- R&D
- Intellectual Property
- Life Sciences
- Materials
- Tech Scout
- Unparalleled Data Quality
- Higher Quality Content
- 60% Fewer Hallucinations
Browse by: Latest US Patents, China's latest patents, Technical Efficacy Thesaurus, Application Domain, Technology Topic, Popular Technical Reports.
© 2025 PatSnap. All rights reserved.Legal|Privacy policy|Modern Slavery Act Transparency Statement|Sitemap|About US| Contact US: help@patsnap.com